Porous array of BaLi4 alloy microchannels enforced carbon cloth for a stable Li composite anode
Abstract
Integrating metallic lithium (Li) with a three-dimensional (3D) host is a popular strategy for long-life Li composite anodes, where the structure and physicochemical nature of the framework are critical for the electrochemical performance. Herein, Li-rich dual-phase barium (Ba)-based alloy composed of BaLi4 intermetallic compounds and Li metal phases is thermally incorporated into commercial carbon cloth sheets to develop Li-Ba alloy composite (LBAC) anodes featuring a porous array of BaLi4 microchannels as the built-in 3D skeleton. Doping of metallic Ba can greatly lower the surface tension of liquid Li and improve the wettability of the molten Li-Ba alloy toward the carbon cloth substrate. Moreover, LBAC benefits from the superior lithiophilicity and the porous architecture of BaLi4 skeleton nested in a conductive carbon fiber matrix, leading to stable cycling performance by confining Li stripping/plating in microchannels network of BaLi4 alloy framework and dissipating high current densities. As a result, the LBAC symmetrical cells can run stably for 1,000 h under 1 mA cm-2 and 1 mA h cm-2, and the capacity retention can retain 93.3% after 300 cycles in the full cell with areal capacity of 2.45 mA h cm-2. This work offers a smart designing strategy of 3D Li alloy composite anodes by introducing porous and lithiophilic alloy scaffold as sub-framework of the carbon hosting anode, promising the prospect of Li metal batteries for future applications.
Keywords
INTRODUCTION
Lithium (Li) metal has high specific capacity (3,860 mA h g-1) and the lowest electrochemical potential
Remarkably, the liquid Li has high surface tension and the poor lithiophilicity of carbon materials causes the liquid Li to display a spherical shape on the most carbon-based substrates, indicating the molten Li is difficult to diffuse into the interior of the carbon-based skeleton, which poses an obstacle for the fabrication of Li composite anodes[28-31]. Therefore, further modification of carbon-based hosts is required to tune the wettability. Apparently, the binding energy among Li atoms can be reduced by some substances that can react with Li metal to form Li compounds or alloys, thus decreasing the surface tension of molten Li and improving the wettability[32]. Coating lithiophilic layers have been widely employed to decorate the carbon-based framework[33-40]. For example, Zhu et al. reported a carbon scroll, which consists of vertically aligned carbon fibers decorated with copper oxide (CuOx) nanoparticles[33]. The CuOx can react with metallic Li to produce Cu and Li2O chemically, which facilitates the wettability of liquid Li to carbon scroll, thus enabling Li metal to be well accommodated inside the skeleton. Alternatively, Wang et al. coated carbon cloth (CC) with ZnO nanoarray to obtain 3D porous hosts[41]. Molten Li can be infiltrated into such a 3D host rapidly due to the enhanced wettability of liquid Li toward 3D porous CC@ZnO. Notably, the nano-scale ZnO coating not only offers the driving force for wettability but also enables the formation of a Li-Zn alloy, exhibiting an exceptionally high Li+ diffusion coefficient and facilitating the uniform Li deposition. However, the Li2O in situ deduced from metal oxide layers can increase the interfacial impedance and prevent the substrate from being perfectly wetted by the molten Li[28]. To avoid this shortcoming, the non-metallic or metallic species that can react with liquid Li to produce Li2O-free Li alloy have been investigated[42-45]. Zhang et al. introduced Si nanowire arrays on commercial CC sheets to fabricate a lithiophilic host[42]. The Si nanowires enhanced the wettability due to the generation of Li22Si5. The same phenomenon is repeated by Ag-coated framework. Zhang et al. found that Ag nanoparticles react with Li to produce Li-Ag alloy, which shows favorable Li affinity[45]. In addition, Ag nanoparticles can also act as the lithiophilic sites, promoting the Li nucleation process uniformly. On the other hand, regulating the micro/nanostructure on the surface of the carbon-derived substrate is also a promising strategy to improve the wettability[46-51]. Feng et al. introduced inactive transition metal nanoparticles (Ni, Cu) onto the surface of CC sheets to form capillary-like structure with conical gaps[47]. When the modified CC was in contact with liquid Li, the generated Laplace pressure forced the molten Li to diffuse into the CC at 220 °C, thereby significantly improving the wettability. It should be pointed out that the radial length of these lithiophilic architectures anchored on carbon-based substrate is only a few micrometers, which has relatively low specific area and is susceptible to being buried by the deposited Li, especially under a high Li plating capacity. This indicates that the conventional host has a limited ability to promote the Li stripping/plating behavior, and Li dendrites will grow uncontrollably on the electrode surface after multiple cycles[38,52]. Therefore, it is essential to design a continuous network of the lithiophilic species with the micro/nano-scale pores as the sub-skeleton, which can not only confine the Li deposition/dissolution behavior in the limited space but also tackle the wettability issue of the carbon-based primary framework, leading to the improved performance of Li composite anodes.
Recently, it has been shown that generating Li-rich Li-X (where X denotes metallic element) alloy by doping other metals into liquid Li can significantly facilitate rapid spreading of molten Li by reducing surface tension[53-55]. In addition, the formed Li alloy phase can act as a 3D framework to regulate Li stripping/plating process for prolonged cyclic lifetime. The geometric structure and physicochemical nature of the Li alloy framework are critical for advanced performance of Li composite anodes. Our group found that dual-phase Li-barium (Ba) alloy has a unique micro-sized ordered array of BaLi4 microchannels, which can homogenize Li+ flux and provide active sites for inducing the uniform Li deposition[56]. However, the long-term cyclic stability cannot be guaranteed due to the insufficient robustness of the Li-Ba alloy scaffold.
Herein, we infiltrate the molten Li-rich Li-Ba alloy composed of BaLi4 intermetallic compounds and Li metal phases into the CC sheet to fabricate a Li-Ba alloy composite anode (named LBAC). Doping of metallic Ba can significantly lower the binding force among Li atoms, allowing the molten liquid alloy to diffuse rapidly into the CC host. In addition, the BaLi4 alloy scaffold is in situ created by phase separation during the cooling process. The porous architecture of BaLi4 skeleton with strong lithiophilicity is nested in conductive carbon fiber network as the sub-framework, which provides larger surface area for the nucleation of Li and confines Li stripping/plating in microchannels of BaLi4 alloy framework, thus suppressing the Li dendrite growth efficiently. Moreover, the structural stability of the Li-Ba alloy is enhanced by the strong flexibility exhibited by the CC. As a result, the LBAC anode displays favorable cycling performance, achieving ultra-long cycle lifespan (> 1,000 h) at 1 mA cm-2 and 1 mA h cm-2 in a symmetric cell with carbonate-based electrolyte. The LBAC/LiFePO4 (LFP) full cell also displays outstanding long-term cycling lifespan and rate performance.
EXPERIMENTAL
Fabrication of LBAC electrode
The stainless steel (SS) foil was utilized as a substrate for the combination of metallic Li (99.5%, Chengdu Denway Newtype Metal Material Co., Ltd) and Ba (99.5%, Aladdin), with a molar ratio of 1:25. Then, the temperature was raised to 400 °C. A circular CC sheet measuring 12 mm in diameter was placed on the molten Li-Ba alloy after the complete dissolution of metallic Ba into liquid Li. The liquid Li-Ba alloy was quickly infiltrated into the CC sheet. Finally, the LBAC electrode was fabricated via a quick cooling treatment. All the operations were performed in an argon-filled glove box (Mikrouna, O2 < 0.01 ppm,
Materials characterization
The LBAC anode and CC were recorded by X-ray diffraction (XRD) from 10 to 90° at 5° min-1 (Cu Kα, 0.15456 nm). The anode morphology was characterized using field emission scanning electron microscopy (FE-SEM) with an acceleration voltage of 20 kV.
Electrochemical measurements
The CR2032-type coin cells were utilized for the assembly of all cells, which were subsequently subjected to testing on a CT2001A battery testing system (LAND Electronic Co. Ltd.) at 25 °C. The working electrodes of symmetrical cells were LBAC, Li-C, or Li-Ba sheets. To standardize, symmetric cells were prepared using an electrolyte containing 100 μL of LiPF6 (1 M) dissolved in a mixture of ethylene carbonate and diethyl carbonate (EC/DEC, v:v = 1:1), supplemented with 5% fluoroethylene carbonate (FEC). As a separator, Celgard 2325 membranes were used. A CHI660C electrochemical workstation (Shanghai, Chenhua) measured electrochemical impedance spectra (EIS) in a frequency range of 0.1 Hz to 1 MHz.
Full cells were assembled using LFP cathodes, a Celgard 2325 separator, and a Li composite anode (Li-C,
RESULTS AND DISCUSSION
The LBAC electrode is obtained by contacting CC disk with molten Li-Ba alloy. As shown in Figure 1A, when the CC touches the liquid Li-Ba alloy, the silver-white molten Li-Ba alloy can fill up the entire CC in less than 10 s, indicating that doping of metallic Ba can significantly lower the surface tension of liquid Li and improve the wettability toward CC. Based on the phase diagram of Li-Ba [Supplementary Figure 1], we can observe that phase segregated Li-Ba dual-phase alloy is composed of BaLi4 intermetallic compounds and Li metal when the Li atomic percentage is larger than 80% and the temperature is lower than 143 °C. Thus, phase separation occurs when the temperature cools rapidly below 143 °C. On the contrary, the CC itself exhibits poor wettability towards liquid Li, so the Li metal does not diffuse into the CC in more than 60 s under the same conditions [Supplementary Figure 2A]. Notably, molten Li-Ba alloy exhibits more favorable wettability than other Li alloys (such as Li-Ca and Li-Ag)[57], which is one of the important merits considering the practical application. The top surface of LBAC is dark gray with the distinct textile pattern of the carbon fibers. As depicted in the top-view scanning electron microscopy (SEM) images
Figure 1. (A) Optical images of the liquid Li-Ba alloy infusion at 400 °C to CC. The top surface morphology of the (B) CC and the
The Li stripping/plating behaviors of LBAC were conducted by SEM so as to analyze the function of BaLi4 alloy sub-scaffold. After 10 mA h cm-2 Li was stripped, the internal porous array was further exposed, and the BaLi4 microchannels array was evidenced as a secondary scaffold in the CC framework [Figure 2A]. As the Li stripping capacity reaches 20 mA h cm-2, the ordered array of BaLi4 alloy microchannels is uniformly dispersed on the carbon fibers, providing a large number of Li nucleation sites and facilitating Li ion diffusion [Supplementary Figure 5]. Furthermore, the lithiophilic Li-Ba alloy can reduce Li nucleation overpotential and inhibit Li dendrite generation during the subsequent process of Li plating. Therefore, when the Li is replated at 5 mA h cm-2 [Figure 2B], the plated Li preferentially fills the microchannels in BaLi4 alloy scaffold and no Li dendrite was visualized. The BaLi4 microchannels can confine the deposited Li in a smaller cage, achieving uniform Li deposition behavior. As the Li plating capacity is up to
Figure 2. (A, D, G) The SEM images of LBAC anode following the removal of 10 mA h cm-2 Li, (B, E, H) subsequent deposition
To further evaluate the electrochemical performance for LBAC anodes, symmetrical cells were assembled using LBAC electrodes for assessing electrochemical cycling performances under different current densities. The Li-C/Li-C and Li-Ba/Li-Ba symmetric cells were also assembled separately for comparison to highlight the synergistic effect of the BaLi4 alloy sub-framework and CC framework. As shown in Figure 3A, the time-voltage curve tells that the voltage hysteresis of LBAC cells can stabilize at 30 mV for 1,000 h under
Figure 3. Electrochemical performances of LBAC, Li-Ba and Li-C symmetric cells at various current densities: (A) 1 mA cm-2; 3 mA cm-2; 5 mA cm-2. Nyquist impedance plots of symmetrical cells with LBAC, Li-Ba and Li-C anodes (B) before and (C) after 100 cycles while operating at a condition of 3 mA cm-2/1 mA h cm-2.
EIS were measured to assess the internal stability of symmetric cells, as shown in Figure 3B. The Rct value of Li-Ba (~450 Ω) and Li-C symmetric cells (~550 Ω) is higher compared to LBAC symmetric cells before cycling (~200 Ω). After 100 cycles, the Rct of the LBAC composite decreases to ~50 Ω, which remains smaller than that of the Li-Ba (75 Ω) and Li-C (125 Ω) cells, indicating that LBAC has faster charge transfer kinetics and a SEI layer with enhanced stability that facilitates reversible process of Li stripping/plating
To acquire a profound comprehension of the function of LBAC on favorable long-term cycling lifespan, morphological evolution of LBAC and Li-C composite electrodes after 100 cycles is investigated, as depicted in Figure 4. After 100 cycles, a quantity of mossy and Li dendrites emerged on the Li-C surface, as illustrated in Figure 4A, delivering a rough and porous Li layer as thick as about 100 μm [Figure 4B and C]. The Li stripping/plating behavior in the LBAC electrode is well regulated by the BaLi4 microchannels array. As shown in Figure 4D, the surface of the deposited Li is smooth, rather than showing Li dendrites, indicating that the favorable lithiophilicity and smaller pores of the BaLi4 sub-scaffold can regulate uniform Li deposition. Figure 4E and F depicts no obvious “dead Li” and Li dendrites on the LABC top surface. Thus, the LBAC with microchannels array can effectively tune the Li growth process and ensure extraordinary cycling stability.
Figure 4. SEM images of (A-C) Li-C and (D-F) LBAC after 100 cycles. The cycling conditions are 3 mA cm-2 and 1 mA h cm-2.
For evaluating the potential application of LBAC anodes in Li metal batteries, the full cells were assembled using LBAC as the anode and high-areal-capacity LFP as the cathode. Additionally, Li-C-based full cells were also assembled. The cycling performance is shown in Figure 5A. In initial cycles, a slight increase of specific capacity occurred in two cells due to the process of activating the electrode. The long-term cycling curve at 1 C demonstrates that the LBAC/LFP cell retains 93.3% of its initial capacity after 300 cycles (equal to 600 h), with a consistently stable coulombic efficiency (CE) of ~99.5%. On the contrary, the capacity retention of the Li-C/LFP full cell is significantly reduced (38.2%) and exhibits a sharp CE fluctuation even within 40 cycles, suffering from continuous capacity decay. Meanwhile, the rate performance was characterized by varying the current rate from 0.1 to 2 C. The LBAC/LFP cell can deliver specific capacities of 155 mA h g-1 (0.1 C), 147 mA h g-1 (0.5 C), and 135 mA h g-1 (1 C), exhibiting superior performance compared to the Li-C/LFP cells (0.1 C:154 mA h g-1, 0.5 C:140 mA h g-1, 1 C:119 mA h g-1), as shown in
CONCLUSIONS
In brief, we have successfully fabricated a remarkably stable Li composite anode with a porous BaLi4 alloy array as the sub-skeleton in the CC sheet for regulating Li stripping/plating behavior via a facile thermal infusion strategy within 10 s. The addition of heteroatomic Ba metal to Li can reduce the surface tension of liquid Li, enhancing the wettability toward the CC. Moreover, the ordered array structure of LBAC anodes not only restricts the Li stripping/plating behavior in the microporous space to suppress Li dendrite growth but also reduces the Li nucleation overpotential to achieve homogeneous Li deposition. Furthermore, the mechanical strength of the anode is significantly enhanced by the excellent flexibility exhibited by the CC host. As a result, the porous array of BaLi4 microchannels nested in CC sheet assists the high cycling performance over 1,000 h under a condition of 1 mA cm-2/1 mA h cm-2 with a dendrite-free morphology. Additionally, a LBAC composite anode exhibits excellent performance in a full cell coupled with a LFP cathode due to the good reversibility and rapid transfer of charge. We believe a composite anode consisting of flexible carbon host architecture and Li-rich Li alloy with built-in lithiophilic and porous skeleton holds great potential as the practical anode material for Li metal batteries.
DECLARATIONS
Authors’ contributions
Contributed substantially to conceptualization, investigation, formal analysis, and writing-original draft: Wang Z
Developed methodology: Chen T
Offered material support: Song Z, Xing J
Provided administration: Zhou A
Made significant contributions to project administration and technical review and editing: Li J
Availability of data and materials
Not applicable.
Financial support and sponsorship
This work was partly supported by the National Natural Science Foundation of China (Nos. 22379019 and 52172184), S&T Special Program of Huzhou (No. 2023GZ03), Huzhou Natural Science Foundation Project (Nos. 2022YZ04 and 2022YZ21), and National Science Foundation of Sichuan Province (No. 2022NSFSC0259).
Conflicts of interest
All authors declared that there are no conflicts of interest.
Ethical approval and consent to participate
Not applicable.
Consent for publication
Not applicable.
Copyright
© The Author(s) 2024.
Supplementary Materials
REFERENCES
1. Park S, Jin HJ, Yun YS. Advances in the design of 3D-structured electrode materials for lithium-metal anodes. Adv Mater 2020;32:2002193.
2. Kang S, Cheng J, Gao W, Cui L. Toward safer lithium metal batteries: a review. Energy Mater 2023;3:300043.
3. Ghazi ZA, Sun Z, Sun C, et al. Key aspects of lithium metal anodes for lithium metal batteries. Small 2019;15:e1900687.
5. Jin C, Sheng O, Chen M, et al. Armed lithium metal anodes with functional skeletons. Mater Today Nano 2021;13:100103.
6. Wang B, Xu T, Huang S, Kong D, Li X, Wang Y. Recent advances in carbon-shell-based nanostructures for advanced Li/Na metal batteries. J Mater Chem A 2021;9:6070-88.
7. Wang C, Wang A, Ren L, et al. Controlling Li ion flux through materials innovation for dendrite-free lithium metal anodes. Adv Funct Mater 2019;29:1905940.
8. Zhao Y, Ye Y, Wu F, Li Y, Li L, Chen R. Anode interface engineering and architecture design for high-performance lithium-sulfur batteries. Adv Mater 2019;31:e1806532.
9. Peng HJ, Xu WT, Zhu L, et al. 3D carbonaceous current collectors: the origin of enhanced cycling stability for high-sulfur-loading lithium - sulfur batteries. Adv Funct Mater 2016;26:6351-8.
10. Shi J, Nguyen HD, Chen Z, et al. Nanostructured block copolymer single-ion conductors for low-temperature, high-voltage and fast charging lithium-metal batteries. Energy Mater 2023;3:300036.
11. Zhong Y, Cao C, Tadé MO, Shao Z. Ionically and electronically conductive phases in a composite anode for high-rate and stable lithium stripping and plating for solid-state lithium batteries. ACS Appl Mater Interfaces 2022;14:38786-94.
12. Yue XY, Wang WW, Wang QC, et al. Cuprite-coated Cu foam skeleton host enabling lateral growth of lithium dendrites for advanced Li metal batteries. Energy Stor Mater 2019;21:180-9.
13. Wang R, Shi F, He X, et al. Three-dimensional lithiophilic Cu@Sn nanocones for dendrite-free lithium metal anodes. Sci China Mater 2021;64:1087-94.
14. Wang Z, Xue J, Liu Y, et al. LixCu alloy nanowires nested in Ni foam for highly stable Li metal composite anode. Sci China Mater 2022;65:69-77.
15. Chi SS, Liu Y, Song WL, Fan LZ, Zhang Q. Prestoring lithium into stable 3D nickel foam host as dendrite-free lithium metal anode. Adv Funct Mater 2017;27:1700348.
16. Eom JY, Choi SH, Kang JH, Eom GH, Moon J, Park MS. Rational design of a 3D Li-metal electrode for high-energy lithium batteries. ACS Appl Energy Mater 2021;4:1936-41.
17. Jia W, Wang Y, Qu S, et al. ZnF2 coated three dimensional Li-Ni composite anode for improved performance. J Materiomics 2019;5:176-84.
18. Huang G, Chen S, Guo P, et al. In situ constructing lithiophilic NiFx nanosheets on Ni foam current collector for stable lithium metal anode via a succinct fluorination strategy. Chem Eng J 2020;395:125122.
19. Wang Q, Yang C, Yang J, et al. Stable Li metal anode with protected interface for high-performance Li metal batteries. Energy Stor Mater 2018;15:249-56.
20. Li X, Yang G, Zhang S, Wang Z, Chen L. Improved lithium deposition on silver plated carbon fiber paper. Nano Energy 2019;66:104144.
21. Xiao J, Xiao N, Liu C, et al. In situ growing chromium oxynitride nanoparticles on carbon nanofibers to stabilize lithium deposition for lithium metal anodes. Small 2020;16:2003827.
22. Chen X, Lv Y, Shang M, Niu J. Ironing controllable lithium into lithiotropic carbon fiber fabric: a novel Li-metal anode with improved cyclability and dendrite suppression. ACS Appl Mater Interfaces 2019;11:21584-92.
23. Jia W, Chen T, Wang Y, et al. Porous equipotential body with heterogeneous nucleation sites: a novel 3D composite current collector for lithium metal anode. Electrochim Acta 2019;309:460-8.
24. Luo L, Li J, Yaghoobnejad Asl H, Manthiram A. A 3D lithiophilic Mo2N-modified carbon nanofiber architecture for dendrite-free lithium-metal anodes in a full cell. Adv Mater 2019;31:e1904537.
25. Wang Z, Deng Q, Song Z, et al. Ultrathin Li-rich Li-Cu alloy anode capped with lithiophilic LiC6 headspace enabling stable cyclic performance. J Colloid Interface Sci 2023;643:205-13.
26. Niu J, Yang J, Channa AI, et al. Enhancing the water splitting performance via decorating Co3O4 nanoarrays with ruthenium doping and phosphorization. RSC Adv 2020;10:27235-41.
27. Wang Y, Shen Y, Du Z, et al. A lithium-carbon nanotube composite for stable lithium anodes. J Mater Chem A 2017;5:23434-9.
28. Zheng ZJ, Ye H, Guo ZP. Recent progress in designing stable composite lithium anodes with improved wettability. Adv Sci 2020;7:2002212.
29. Wang SH, Yue J, Dong W, et al. Tuning wettability of molten lithium via a chemical strategy for lithium metal anodes. Nat Commun 2019;10:4930.
30. Wang J, Wang H, Xie J, et al. Fundamental study on the wetting property of liquid lithium. Energy Stor Mater 2018;14:345-50.
31. Shin HJ, Abbas S, Kim J, Cho J, Ha HY. Near-perfect suppression of Li dendrite growth by novel porous hollow carbon fibers embedded with ZnO nanoparticles as stable and efficient anode for Li metal batteries. Chem Eng J 2023;464:142713.
32. Niu C, Pan H, Xu W, et al. Self-smoothing anode for achieving high-energy lithium metal batteries under realistic conditions. Nat Nanotechnol 2019;14:594-601.
33. Zhu R, Yang H, Fadillah L, et al. A lithiophilic carbon scroll as a Li metal host with low tortuosity design and “Dead Li” self-cleaning capability. J Mater Chem A 2021;9:13332-43.
34. Yue XY, Li XL, Wang WW, et al. Wettable carbon felt framework for high loading Li-metal composite anode. Nano Energy 2019;60:257-66.
35. Wang L, Zhu X, Guan Y, et al. ZnO/carbon framework derived from metal-organic frameworks as a stable host for lithium metal anodes. Energy Stor Mater 2018;11:191-6.
36. Le T, Yang C, Liang Q, Huang X, Kang F, Yang Y. A fishing-net-like 3D host for robust and ultrahigh-rate lithium metal anodes. Small 2021;17:e2007231.
37. Chen XR, Li BQ, Zhu C, et al. A coaxial-interweaved hybrid lithium metal anode for long-lifespan lithium metal batteries. Adv Energy Mater 2019;9:1901932.
38. Deng W, Zhu W, Zhou X, Peng X, Liu Z. Highly reversible Li plating confined in three-dimensional interconnected microchannels toward high-rate and stable metallic lithium anodes. ACS Appl Mater Interfaces 2018;10:20387-95.
39. Cao J, Xie Y, Li W, et al. Rationally optimized carbon fiber cloth as lithiophilic host for highly stable Li metal anodes. Mater Today Energy 2021;20:100663.
40. Gong YJ, Pyo S, Kim H, et al. Advanced Li metal anode by fluorinated metathesis on conjugated carbon networks. Energy Environ Sci 2021;14:940-54.
41. Wang X, Pan Z, Wu Y, et al. Infiltrating lithium into carbon cloth decorated with zinc oxide arrays for dendrite-free lithium metal anode. Nano Res 2019;12:525-9.
42. Zhang P, Peng C, Liu X, et al. 3D lithiophilic “Hairy” Si nanowire arrays @ carbon scaffold favor a flexible and stable lithium composite anode. ACS Appl Mater Interfaces 2019;11:44325-32.
43. Zhang YJ, Liu SF, Wang XL, et al. Composite Li metal anode with vertical graphene host for high performance Li-S batteries. J Power Sources 2018;374:205-10.
44. Liu T, Hu J, Li C, Wang Y. Unusual conformal Li plating on alloyable nanofiber frameworks to enable dendrite suppression of Li metal anode. ACS Appl Energy Mater 2019;2:4379-88.
45. Zhang R, Chen X, Shen X, et al. Coralloid carbon fiber-based composite lithium anode for robust lithium metal batteries. Joule 2018;2:764-77.
46. Go W, Kim MH, Park J, et al. Nanocrevasse-rich carbon fibers for stable lithium and sodium metal anodes. Nano Lett 2019;19:1504-11.
47. Feng YQ, Zheng ZJ, Wang CY, et al. A super-lithiophilic nanocrystallization strategy for stable lithium metal anodes. Nano Energy 2020;73:104731.
48. Fang Y, Zhang Y, Zhu K, et al. Lithiophilic three-dimensional porous Ti3C2Tx-rGO membrane as a stable scaffold for safe alkali metal (Li or Na) anodes. ACS Nano 2019;13:14319-28.
49. Liu S, Xia X, Zhong Y, et al. 3D TiC/C core/shell nanowire skeleton for dendrite-free and long-life lithium metal anode. Adv Energy Mater 2018;8:1702322.
50. Kwon H, Lee JH, Roh Y, et al. An electron-deficient carbon current collector for anode-free Li-metal batteries. Nat Commun 2021;12:5537.
51. Patrike A, Suresh K, Wahid M, Chaturvedi V, Shelke MV. Ice-colloidal templated carbon host for highly efficient, dendrite free Li metal anode. Carbon 2021;179:256-65.
52. Pathak R, Chen K, Wu F, et al. Advanced strategies for the development of porous carbon as a Li host/current collector for lithium metal batteries. Energy Stor Mater 2021;41:448-65.
53. Wang C, Xie H, Zhang L, et al. Universal soldering of lithium and sodium alloys on various substrates for batteries. Adv Energy Mater 2018;8:1701963.
54. Yang C, Xie H, Ping W, et al. An electron/ion dual-conductive alloy framework for high-rate and high-capacity solid-state lithium-metal batteries. Adv Mater 2019;31:e1804815.
55. Jia W, Wang Z, Li J, et al. A dual-phase Li-Ca alloy with a patternable and lithiophilic 3D framework for improving lithium anode performance. J Mater Chem A 2019;7:22377-84.
56. Jia W, Chen J, Wang Z, Zhou A, Hu YS, Li J. Dendrite-free dual-phase Li-Ba alloy anode enabled by ordered array of built-in mixed conducting microchannels. Small 2023:2308279.
Cite This Article
Export citation file: BibTeX | RIS
OAE Style
Wang Z, Chen T, Song Z, Xing J, Zhou A, Li J. Porous array of BaLi4 alloy microchannels enforced carbon cloth for a stable Li composite anode. Energy Mater 2024;4:400031. http://dx.doi.org/10.20517/energymater.2023.103
AMA Style
Wang Z, Chen T, Song Z, Xing J, Zhou A, Li J. Porous array of BaLi4 alloy microchannels enforced carbon cloth for a stable Li composite anode. Energy Materials. 2024; 4(3): 400031. http://dx.doi.org/10.20517/energymater.2023.103
Chicago/Turabian Style
Wang, Zihao, Tao Chen, Zhicui Song, Jianxiong Xing, Aijun Zhou, Jingze Li. 2024. "Porous array of BaLi4 alloy microchannels enforced carbon cloth for a stable Li composite anode" Energy Materials. 4, no.3: 400031. http://dx.doi.org/10.20517/energymater.2023.103
ACS Style
Wang, Z.; Chen T.; Song Z.; Xing J.; Zhou A.; Li J. Porous array of BaLi4 alloy microchannels enforced carbon cloth for a stable Li composite anode. Energy Mater. 2024, 4, 400031. http://dx.doi.org/10.20517/energymater.2023.103
About This Article
Special Issue
Copyright
Data & Comments
Data
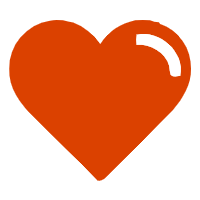

Comments
Comments must be written in English. Spam, offensive content, impersonation, and private information will not be permitted. If any comment is reported and identified as inappropriate content by OAE staff, the comment will be removed without notice. If you have any queries or need any help, please contact us at support@oaepublish.com.