Protective behavior of phosphonate-functionalized imidazolium ionic liquid and its impact on the Li-ion battery performance
Abstract
The commercial lithium-ion batteries (LIBs) rely on lithium hexafluorophosphate (LiPF6), which is extremely sensitive to moisture and liable to thermal decomposition. Lithium bis (trifluoro methane sulfonyl) imide (LiTFSI), as a promising electrolyte salt, possesses high thermal stability and excellent moisture tolerance. However, LiTFSI is closely related to severe corrosion of the aluminum (Al) current collector at high voltage. Herein, phosphonate-functionalized imidazolium ionic liquid (PFIL) is developed and utilized as an electrolyte co-solvent to inhibit the oxidative dissolution of the Al current collector. PFIL can suppress Al corrosion by participating in the interface reaction and forming a stable and reliable protective film on the surface of Al foils, as confirmed by X-ray photoelectron spectroscopy. Thanks to the corrosion suppression of the Al current collector, the
Keywords
INTRODUCTION
Lithium hexafluorophosphate (LiPF6) is the most widely used lithium salt for commercial lithium-ion batteries (LIBs)[1]. However, the LiPF6 salt is extremely sensitive to moisture and susceptible to thermal decomposition (125 oC)[2-5]. The decomposition product of phosphorus pentafluoride (PF5) of LiPF6 is a strong Lewis acid[6,7], which initiates the decomposition of cyclic carbonate. When PF5 reacts with a trace amount of water, active hydrogen fluoride (HF) will corrode a solid electrolyte interphase (SEI) layer, dissolve the cathode, and deteriorate the electrochemical performance of the LIBs[8-11].
To overcome these problems, researchers are devoted to seeking a stable lithium salt to replace LiPF6[12-15]. Because of excellent thermal and moisture stability (360 oC), high ionic conductivity, and good electrochemical stability, lithium bis (trifluoro methane sulfonyl) imide (LiTFSI) is considered as a promising electrolyte salt for use in the LIBs[12,16,17]. The operation temperature range and safety performance of the LIBs are enhanced by using LiTFSI instead of LiPF6. For these reasons, intensive studies have been conducted on the LiTFSI-based electrolyte[18-21]. However, the application of LiTFSI is constrained by severe corrosion of the Al current collector (~3.7 V vs. Li/Li+)[22-24]. The urgent resolution of the corrosion issue of the Al current collector becomes more imperative when it is matched with high-voltage cathode materials.
The LiTFSI-based electrolyte causes continuous dissolution of alumina and aluminum (Al) because it fails to form an effective passivation layer on the Al current collector[25]. The corrosion of the Al current collector can be partially alleviated by adjusting the proportion of lithium salts and utilization of functional additives to form a protective layer over the Al current collector. Matsumoto et al. proposed that high concentration LiTFSI (1.8 M) electrolyte formed a LiF passivation layer on Al current collector, which could inhibit the corrosion[26]. Li et al. proved the formation of a boron-based passivation layer by oxidative decomposition of lithium difluoro(oxalate)borate (LiODFB) to suppress the dissolution of Al current collectors[23]. Although these additives can mitigate the corrosion of Al current collectors, their practical application is limited due to their incompatibility with positive electrode materials, resulting in poor electrochemical stability at high potentials.
Ionic liquids (ILs) show various unique properties, such as non-flammability, non-volatility, and wide high-voltage stability window, which are considered as ideal high-potential electrolyte additives to replace part of the organic carbonates[27,28]. Peng et al. suggested that the Al current collector was stable in the IL electrolyte, which was attributed to a good passivation layer formed by the oxidation between Al and the anions of the IL electrolyte[29]. Therefore, ILs are expected to have the ability to suppress the Al current collector corrosion.
Among various types of ILs, imidazolium-based ILs are the most studied due to their low viscosity and high conductivity[30]. Nevertheless, the acidic hydrogen at the C2 position of the imidazole ring is easily protonated, resulting in poor cathodic stability[31]. According to previous research, this problem was ameliorated by the introduction of phosphorus functional groups[32]. The use of phosphonate-functionalized ILs (PFILs) is proposed in this work as an electrolyte co-solvent to suppress the oxidative dissolution of the Al current collector. The impact of the PFILs on the electrochemical properties of the high-voltage Li||LiNi0.8Co0.1Mn0.1O2 (Li||NCM811) cell is investigated to reveal the working mechanism of the PFILs. The cathodic aluminum dissolution mechanism in the electrolytes with and without PFILs is shown in Figure 1. After cycling, the TFSI- anion attacks the Al2O3 passivation layer on fresh Al foils to form the corrosion product Al-TFSI compounds[1,13,33] [Figure 1B]. On the contrary, after adding PFIL, a protective layer dominated by LixPOyFz is generated on the surface of Al foils, which can prevent Al corrosion caused by LiTFSI [Figure 1C].
EXPERIMENTAL
Materials
Bis (trifluoro methane sulfone) imide lithium salt (LiTFSI, 99.9%), ethylene carbonate (EC), and dimethyl carbonate (DMC), diethyl (3-bromopropyl) phosphonate (95%), 1-hexylimidazole (99%), ethyl acetate (EtOAc, 99%), dichloromethane (CH2Cl2, 99%), Silver nitrate (AgNO3, 99%), and N-methyl-2-pyrrolidone (NMP, 99%) were purchased from Macklin. LiNi0.8Mn0.1Co0.1O2 (NCM811), poly (vinylidene fluoride) (PVDF), and conductive carbon black (Super P) were purchased from Guangdong Canrd New Energy Technology Co., Ltd.
Preparation of PFIL
The synthetic route of PFIL is shown in Figure 2. Detailed synthetic steps are shown in the Supplementary Material.
Structural characterization of PFIL
Fourier transform infrared spectroscopy (FT-IR) was recorded on a Nicolet 6700 FT-IR spectrometer (Thermo Fisher). 31P nuclear magnetic resonance (NMR), 1H NMR, and 13C NMR of PFIL were recorded on a Bruker AV-400 NMR spectrometer in CDCl3. NMR spectrogram analysis is shown in the Supplementary Material. 31P NMR, 1H NMR, and 13C NMR spectra of PFIL are presented in Supplementary Figures 1-3, which confirms the synthesis of the PFIL molecule.
Purity characterization of PFIL
The water content of PFIL was measured by a Karl Fischer moisture meter (870 KF Titrino plus), and the result showed that the water content of PFIL was 0.26% [Supplementary Table 1]. To determine the halide content of PFIL, ion chromatography was conducted using a Thermo Fisher Aquion instrument with the pre-processing method of combustion in an oxygen bomb. The bromine content was found to be less than 50 ppm [Supplementary Figure 4], indicating that the bromide ions were almost completely exchanged during the synthesis process of PFIL.
Electrochemical measurements
The base electrolyte was prepared by dissolving 1.0 M LiTFSI in the solvent mixture of EC and DMC (1:1 by volume). In comparison, the hybrid electrolyte, which contained 20% PFIL and 80% base electrolyte, was prepared in the glove box (Mikrouna, China). To prepare the NCM811 electrode, NCM811 was employed as the active material, super P served as the electron conductive agent, and PVDF acted as the binder. These components were mixed in NMP with a weight ratio of 8:1:1. The slurry was coated onto an Al foil and further dried at 120 oC under vacuum for 24 h. The NCM811 electrode was punched into 12 mm diameter disks for testing and transferred into an Ar-filled glove box for cell assembly.
All electrochemical performances were conducted using the coin cells (CR2032) with lithium foils as the counter electrode, which were assembled in an Ar-filled glove box and operated with a CHI-660E workstation (Chenhua, Shanghai). Galvanostatic charge and discharge measurements were performed on a LAND battery system (Wuhan, China). The cut-off voltages were set to 3.0-4.4 V for the Li||NCM811 half-cell. The AC impedance combined with the chrono-amperometry was applied to examine the lithium (Li)-ion transference number (tLi+). A lithium symmetrical battery was used here. The electrochemical window of the electrolyte was investigated through linear sweep voltammetry (LSV) at room temperature, using a scan rate of 5 mV s-1 within the potential range of 3.0 V to 5.0 V. Cyclic voltammetry (CV) measurements were carried out in the potential range of 2.0-5.0 V for Li||Al half-cell. An AC amplitude of 5 mV was used during the performance of electrochemical impedance spectroscopy (EIS) within a frequency range spanning from 0.01 Hz to 100 KHz. Ionic conductivities measurements were maintained on an FE38-standard (Mettler Toledo, Switzerland). Raman spectra were carried out to indicate the influence of adding PFIL to a base electrolyte.
For the analysis of surface chemistry and morphology of the Al current collector, all cells were disassembled in the glove box. The Al current collector was washed with DMC to remove electrolyte residual and dried at room temperature. The morphology of the Al current collector was observed by scanning electron microscopy (SEM, Hitachi, Japan). The surface chemistry of the Al current collector was examined by X-ray photoelectron spectroscopy (XPS, ESCALAB 250Xi).
RESULTS AND DISCUSSION
As we all know, the conductivity, viscosity, and flammability of the electrolyte are crucial for the performance of the LIBs. Figure 3A shows the viscosity and conductivity change before and after the addition of 20 wt% PFIL. When the temperature increases, the viscosity decreases, and the conductivity increases. Because the viscosity of the PFIL is higher than that of the organic carbonate solvent, the viscosity of the hybrid electrolyte is slightly higher than the base electrolyte, and the conductivity decreases at the same temperature. The conductivity meets the requirements of the LIBs. As shown in Figure 3B, the self-extinguishing time (SET) is used to test the flammability of the electrolyte. With increasing PFIL content, the SET value gradually decreases, which is 174.1 s g-1 when 20 wt% of PFIL is added. With the addition of 80 wt% of PFIL, the electrolyte is completely non-flammable. The results confirm that the PFIL additive can significantly enhance the safety of the electrolyte.
Figure 3. Temperature-dependent ionic conductivity of the electrolyte without PFIL and the electrolyte with 20 wt% of PFIL (A); Self-extinguishing time (SET) of the electrolytes with different PFIL contents (B).
The calculation of the tLi+ was conducted using the Bruce-Vincent-Evans equation. The tLi+ of the hybrid electrolyte is 0.46, which is much higher than that of the base electrolyte (0.35) in Figure 4A and B. The increase of the tLi+ is ascribed to the lone pair electrons of the PFIL cation, which has the ability to strongly coordinate Li-ions.
Figure 4. AC impedance spectra and chrono-amperometry curves of the electrolyte without PFIL (A) and the electrolyte with PFIL (B).
It is well known that the introduction of functional groups in ILs is done to demonstrate their impact on the physicochemical and electrochemical properties of electrolytes through the interaction between the functional groups and Li-ions[34-36]. Raman spectroscopy is applied to detect the changes of ion-ion and ion-solvent interactions in the electrolytes[37-39]. Figure 5A shows the Raman spectra of the interaction of PFIL with LiTFSI. The peak at 747 cm-1 corresponds to the bending vibration of the S-N-S group in LiTFSI, and its intensity significantly increases with the addition of PFIL to the base electrolyte. Moreover, the peak located at 900 cm-1 belongs to symmetrical stretching vibration of the O=S=O group, where the intensity is sightly enhanced with the addition of PFIL. Based on these results, it is clearly indicated that the solvation of Li-ions is caused by the coordination of the phosphonate group on cation, thereby weakening the interaction between Li-ions and bis (trifluoro methane sulfonyl) imide anions. This is the reason for the increased Li-ion transfer number.
Figure 5. Raman spectra of the electrolyte without PFIL and the electrolyte with PFIL (A); LSV voltammograms of the electrolyte without PFIL and the electrolyte with PFIL (B); cyclic voltammetry of the Al electrodes in the electrolyte without PFIL (C) and the electrolyte with PFIL (D), respectively.
The rate performance test is performed at the current density sequence of 0.5 C, 1 C, 2 C, 3 C, and 5 C, respectively [Supplementary Figures 5-7]. Better rate performance is exhibited when PFIL is used. At 0.5 C, the capacity exhibited by the base electrolyte is similar to that of the cell cycled with PFIL. However, the capacity difference is enlarged along with increasing current densities. The cell utilizing the PFIL electrolyte exhibits a capacity of
The electrochemical stabilities of the electrolytes are investigated by LSV. Figure 5B shows the LSV curves of the electrolyte without PFIL and the electrolyte with PFIL. The electrochemical oxidation of the electrolyte with PFIL exhibits an onset voltage of 5.1 V, which is 0.2 V higher compared to the electrolyte without PFIL. As already reported, introducing functionalized group into the cations of the imidazole-based IL could increase the electrochemical stability, which sufficiently improves the electrochemical stability of electrolytes[40]. The phosphonate functional group incorporated into the cation of the imidazole-based ILs enables PFIL to be a promising alternative electrolyte for LIBs.
To investigate the corrosion of Al foils by LiTFSI, CV measurements are applied to the Li||Al cells cycled with the base and hybrid electrolytes, respectively [Figure 5C and D]. At the first scan, the corrosion current of the cells using the base electrolyte begins to rise after 4.2 V. When the amount of PFIL is 20 wt%; the corrosion current begins to rise after 4.6 V. The magnitude of the corrosion current density is significantly different at 5 V. The corrosion current density of the base electrolyte is 1.67 mA cm-2, and the current drops to 0.186 mA cm-2 when PFIL is added to the base electrolyte. The Al foils in the base electrolyte exhibit a higher anodic current density, which indicates severe Al current collector corrosion. Those results can fully explain the inhibition of Al current collector corrosion by PFIL. Meanwhile, to properly evaluate the corrosion inhibition effect of the phosphonium-functionalized imidazolium IL (PFIL), we conducted CV tests on Li||Al batteries using electrolytes containing 20 wt% of non-functionalized imidazolium ILs
To further characterize the corrosion of the Al current collector induced by LiTFSI, the Al foils from the
Figure 6. SEM morphologies of the fresh Al foils (A and B), the Al foils after a CV test in the electrolyte without PFIL (C and D), and the electrolyte with PFIL (E and F).
XPS is applied to analyze the chemical composition at the surface of the Al foils [Figure 7]. For Al 2p spectra [Figure 7A], the peaks at 75.6 eV, 74.6 eV, and 71.9 eV correspond to Al-F, Al2O3, and Al, respectively[1,33]. The peaks of Al2O3 and Al with the hybrid electrolyte are much stronger than the base electrolyte. The Al-F peak is only present on the Al foil after cycling in the basic electrolyte, while it is absent on the Al foil after cycling in the hybrid electrolyte, indicating that the presence of PFIL can suppress the corrosion of the Al current collector by LiTFSI. Moreover, in the O 1s spectra [Figure 7C], the peak assigned to Al2O3
Figure 7. XPS spectra of the Al foils cycled in the electrolyte with PFIL and the electrolyte without PFIL.
According to the above analysis, it is speculated that the TFSI- anion attacks the Al2O3 passivation layer on fresh Al foils to form the corrosion product Al-TFSI compounds. The compounds can be dissolved by the carbonate solvent. With the failure of the Al2O3 passivation layer, Al is exposed to the electrolyte and begins to be dissolved continuously at high potential. On the contrary, after adding PFIL, a protective layer dominated by LixPOyFz is generated on the surface of Al foils, which can prevent Al corrosion caused by LiTFSI according to the SEM results.
The cycling performance of the Li||NCM811 cell is evaluated with four initial cycles at 0.1 C, followed by further cycles at 0.5 C [Figure 8A]. The cell utilizing the base electrolyte exhibits a discharge capacity of
Figure 8. Cycling performance and coulombic efficiency of Li||NCM811 cells with the electrolyte without PFIL and the electrolyte with PFIL (A) with the first four cycles at 0.1 C and following cycles at 0.5 C; Nyquist plots of Li||NCM811 cells cycled in the electrolyte without PFIL (B) and the electrolyte with PFIL (C), respectively.
Performance data of Li‖NCM811 batteries with different electrolytes
Electrolyte | Test condition | Initial discharge specific capacity | Initial coulombic efficiency | After 100 cycles | References |
1M LiTFSI + EC/DMC (1:1) | 1 C = 200 mA/g; 3.0-4.4 V; 0.5 C; 25 oC | 196.1 mAh/g | 89.3% | 16.8% | / |
0.2M PFIL + 0.8M LiTFSI + EC/DMC (1:1) | 1C = 200 mA/g; 3.0-4.4 V; 0.5 C; 25 oC | 204.7 mAh/g | 86.0% | 48.6% | / |
1M LiPF6 + EC/DMC/EMC (1:1:1) | 1 C = 200 mA/g; 2.5-4.5 V; 0.2 C; 25 oC | 198.2 mAh/g | 86.1% | 51.0% | [45] |
1M LiPF6 + EC/DMC (1:2) | 1 C = 200 mA/g; 3.0-4.3 V; 0.5 C; 60 oC | 220.8 mAh/g | 88.1% | 46.4% | [46] |
1M LiPF6 + EC/DEC/EMC (1:1:1) | 1 C = 200 mA/g; 2.7-4.3 V; 1 C; 25 oC | 152.9 mAh/g | / | 78.37% | [47] |
EIS is conducted to further explore the influence of PFIL on the electrochemical performance of the
The impedance data of the battery after different cycles in the electrolyte without PFIL and the electrolyte with PFIL are shown in Table 2. After the first cycle, the Rsei and Rct of the electrolyte with PFIL are slightly higher than that of the electrolyte without PFIL, which may be caused by the formation of a stable interfacial film in the electrolyte with PFIL. As the cycle proceeds, the Rct of the electrolyte without PFIL cells is significantly larger by an order of magnitude after the 10th cycle than the Rct of the electrolyte with PFIL cells. The significant difference is attributed to aluminum corrosion. On the one hand, the corrosion of the collector will make the active material lose electrical contact with the external circuit, which significantly increases the difficulty of electron transfer. On the other hand, the corrosion of Al by LiTFSI causes continuous decomposition of electrolytes and thickens the positive electrode surface film, which leads to the deterioration of positive electrode charge diffusion kinetics.
Fitted data for the EIS spectra of NCM811 cells with and without PFIL
Sample | After one cycle | After ten cycles | After 50 cycles | ||||
R (Ω) | Rsei (Ω) | Rct (Ω) | Rsei (Ω) | Rct (Ω) | Rsei (Ω) | Rct (Ω) | |
With PFIL | 51.04 | 90.29 | 68.10 | 141.20 | 75.8 | 219.1 | |
Without PFIL | 39.86 | 72.33 | 99.56 | 2,236 | 318.8 | 2,946 |
In order to observe the corrosion of the Al current collector caused by LiTFSI, the morphology of the Al current collector of cycled Li||NCM811 cell is characterized by SEM. Before cycling, it is evident that the fresh Al foils [Figure 9A] exhibit a smooth surface. However, after cycling with the base electrolyte, the Al current collector [Figure 9B] shows numerous corrosion holes. The existence of the corrosion holes not only aggravates the polarization of the battery but also leads to rapid attenuation of the battery capacity. In contrast, the Al foils of the cell cycled with the hybrid electrolyte are smooth and flat [Figure 9C]. The inclusion of PFIL is further evidence of its ability to inhibit surface corrosion of the Al current collector caused by LiTFSI over multiple cycles.
CONCLUSIONS
In summary, PFIL is synthesized and utilized as an electrolyte co-solvent in the Li||NCM811 cell. The oxidation dissolution of the Al collector induced by LiTFSI is effectively suppressed by PFIL, resulting in significantly improved cycling and rate performances. The addition of PFIL considerably reduces the corrosion current density from 1.67 mA cm-2 to 0.186 mA cm-2 according to the result of CV, which proves that PFIL inhibits the Al current collector corrosion. The XPS confirms that PFIL is involved in the interface reaction, forming a stable passivation film rich in LixPOyFz on the surface of the Al foil, which can effectively improve Li-ion transportation. The Li||NCM811 cell with the hybrid electrolyte shows a more stable cycling performance than the cell cycled with the base electrolyte. After 100 cycles at 0.5 C, a capacity of
DECLARATIONS
Authors’ contributionsCarried out laboratory research and manuscript writing: Liao K, Song J
Carried out materials testing and characterization: Ge J
Carried out material synthesis: Si J
Contributed to the literature research: Cai Y, Luo Z
Carried out student supervision, concept development, funding acquisition, and manuscript revision: Zhou M, Liang H, Cheng YJ, Milanovic M, Inoishi A, Okada S
Availability of data and materialsAvailable upon request from the authors.
Financial support and sponsorshipThis work was financially supported by the Municipal Key R&D Program of Ningbo (2020Z024, 2021Z121, 2022Z096, 2022Z158, 2022Z115, 2023Z064) and sponsored by K.C. Wong Magna Fund at Ningbo University.
Conflicts of interestAll authors declared that there are no conflicts of interest.
Ethical approval and consent to participateNot applicable.
Consent for publicationNot applicable.
Copyright© The Author(s) 2023.
Supplementary MaterialsREFERENCES
1. Shangguan X, Jia G, Li F, et al. 1-ethyl-3-methyl-imidazolium bis (trifluoromethane-sulfonyl) imide as an electrolyte additive in LiFePO4-based batteries for suppressing aluminum corrosion. Energy Technol 2018;6:1667-74.
2. Liu Z, Chai J, Xu G, Wang Q, Cui G. Functional lithium borate salts and their potential application in high performance lithium batteries. Coord Chem Rev 2015;292:56-73.
3. Li J, Xie K, Lai Y, et al. Lithium oxalyldifluoroborate/carbonate electrolytes for LiFePO4/artificial graphite lithium-ion cells. J Power Sources 2010;195:5344-50.
4. Kaymaksiz S, Wilhelm F, Wachtler M, et al. Electrochemical stability of lithium salicylato-borates as electrolyte additives in Li-ion batteries. J Power Sources 2013;239:659-69.
5. Li S, Zhao W, Zhou Z, et al. Studies on electrochemical performances of novel electrolytes for wide-temperature-range lithium-ion batteries. ACS Appl Mater Inter 2014;6:4920-6.
6. Andersson AM, Edström K. Chemical composition and morphology of the elevated temperature SEI on graphite. J Electrochem Soc 2001;148:A1100.
7. Sloop SE, Pugh JK, Wang S, Kerr JB, Kinoshita K. Chemical reactivity of PF5 and LiPF6 in ethylene carbonate/dimethyl carbonate solutions. ECS Solid State Lett 2001;4:A42.
8. Kanamura K, Takezawa H, Shiraishi S, Takehara Z. Chemical reaction of lithium surface during immersion in LiClO4 or LiPF6/DEC electrolyte. J Electrochem Soc 1997;144:1900-6.
9. Zhou G, Sun X, Li QH, et al. Mn Ion dissolution mechanism for lithium-ion battery with LiMn2O4 cathode: in situ ultraviolet-visible spectroscopy and Ab initio molecular dynamics simulations. J Phys Chem Lett 2020;11:3051-7.
10. Lin C, Tang A, Mu H, Wang W, Wang C. Aging mechanisms of electrode materials in lithium-ion batteries for electric vehicles. J Chem 2015;2015:104673.
11. Tebbe JL, Fuerst TF, Musgrave CB. Mechanism of hydrofluoric acid formation in ethylene carbonate electrolytes with fluorine salt additives. J Power Sources 2015;297:427-35.
12. Dahbi M, Ghamouss F, Tran-van F, Lemordant D, Anouti M. Comparative study of EC/DMC LiTFSI and LiPF6 electrolytes for electrochemical storage. J Power Sources 2011;196:9743-50.
13. Gabryelczyk A, Ivanov S, Bund A, Lota G. Corrosion of aluminium current collector in lithium-ion batteries: a review. J Energy Storage 2021;43:103226.
14. Bushkova OV, Yaroslavtseva TV, Dobrovolsky YA. New lithium salts in electrolytes for lithium-ion batteries (Review). Russ J Electrochem 2017;53:677-99.
15. Bizot C, Blin M, Guichard P, et al. Aluminum current collector for high voltage Li-ion battery. Part I: a benchmark study with statistical analysis. Electrochem Commun 2021;126:107013.
16. Naoi K, Mori M, Naruoka Y, Lamanna WM, Atanasoski R. The surface film formed on a lithium metal electrode in a new imide electrolyte, lithium bis(perfluoroethylsulfonylimide) [LiN(C2F5SO2)2]. J Electrochem Soc 1999;146:462.
17. Han H, Zhou S, Zhang D, et al. Lithium bis(fluorosulfonyl)imide (LiFSI) as conducting salt for nonaqueous liquid electrolytes for lithium-ion batteries: physicochemical and electrochemical properties. J Power Sources 2011;196:3623-32.
18. Meister P, Qi X, Kloepsch R, et al. Anodic behavior of the aluminum current collector in imide-based electrolytes: influence of solvent, operating temperature, and native oxide-layer thickness. ChemSusChem 2017;10:804-14.
19. Yen C, Neale AR, Lim J, Bresser D, Hardwick LJ, Hu C. Corrosion suppression of aluminium current collectors within Li-ion cells using 3-methoxypropionitrile-based electrolytes. Electrochim Acta 2022;431:141105.
20. Abouimrane A, Ding J, Davidson I. Liquid electrolyte based on lithium bis-fluorosulfonyl imide salt: aluminum corrosion studies and lithium ion battery investigations. J Power Sources 2009;189:693-6.
21. Dahbi M, Ghamouss F, Tran-van F, Lemordant D, Anouti M. Ester based electrolyte with lithium bis(trifluoromethane sulfonyl) imide salt for electrochemical storage devices: physicochemical and electrochemical characterization. Electrochim Acta 2012;86:287-93.
22. Chen X, Xu W, Engelhard MH, et al. Mixed salts of LiTFSI and LiBOB for stable LiFePO4-based batteries at elevated temperatures. J Mater Chem A 2014;2:2346.
23. Li F, Gong Y, Jia G, et al. A novel dual-salts of LiTFSI and LiODFB in LiFePO4-based batteries for suppressing aluminum corrosion and improving cycling stability. J Power Sources 2015;295:47-54.
24. Pan Y, Wang G, Lucht BL. Cycling performance and surface analysis of lithium bis(trifluoromethanesulfonyl)imide in propylene carbonate with graphite. Electrochim Acta 2016;217:269-73.
25. Krämer E, Schedlbauer T, Hoffmann B, et al. Mechanism of anodic dissolution of the aluminum current collector in 1 M LiTFSI EC:DEC 3:7 in rechargeable lithium batteries. J Electrochem Soc 2013;160:A356.
26. Matsumoto K, Inoue K, Nakahara K, Yuge R, Noguchi T, Utsugi K. Suppression of aluminum corrosion by using high concentration LiTFSI electrolyte. J Power Sources 2013;231:234-8.
27. Li R, Fang Z, Wang C, et al. Six-armed and dicationic polymeric ionic liquid for highly stretchable, nonflammable and notch-insensitive intrinsic self-healing solid-state polymer electrolyte for flexible and safe lithium batteries. Chem Eng J 2022;430:132706.
28. Wang B, Wang G, He P, Fan L. Rational design of ultrathin composite solid-state electrolyte for high-performance lithium metal batteries. J Membr Sci 2022;642:119952.
29. Peng C, Yang L, Zhang Z, Tachibana K, Yang Y, Zhao S. Investigation of the anodic behavior of Al current collector in room temperature ionic liquid electrolytes. Electrochim Acta 2008;53:4764-72.
30. Liu K, Wang Z, Shi L, Jungsuttiwong S, Yuan S. Ionic liquids for high performance lithium metal batteries. J Energy Chem 2021;59:320-33.
31. Tang X, Lv S, Jiang K, Zhou G, Liu X. Recent development of ionic liquid-based electrolytes in lithium-ion batteries. J Power Sources 2022;542:231792.
32. Ge J, Liang H, Zhou M, et al. Phosphonate-functionalized ionic liquid: a novel electrolyte additive for eenhanced cyclic stability and rate capability of LiCoO2 cathode at high voltage. ChemistrySelect 2019;4:9959-65.
33. Morita M, Shibata T, Yoshimoto N, Ishikawa M. Anodic behavior of aluminum in organic solutions with different electrolytic salts for lithium ion batteries. Electrochim Acta 2002;47:2787-93.
34. Mai YJ, Luo H, Zhao XY, et al. Organosilicon functionalized quaternary ammonium ionic liquids as electrolytes for lithium-ion batteries. Ionics 2014;20:1207-15.
35. Fei Z, Geldbach TJ, Zhao D, Dyson PJ. From dysfunction to bis-function: on the design and applications of functionalised ionic liquids. Chemistry 2006;12:2122-30.
37. Seo DM, Borodin O, Han S, Boyle PD, Henderson WA. Electrolyte solvation and ionic association II. acetonitrile-lithium salt mixtures: highly dissociated salts. J Electrochem Soc 2012;159:A1489.
38. Seo DM, Borodin O, Han S, Ly Q, Boyle PD, Henderson WA. Electrolyte solvation and ionic association. J Electrochem Soc 2012;159:A553.
39. Umebayashi Y, Mitsugi T, Fukuda S, et al. Lithium ion solvation in room-temperature ionic liquids involving bis(trifluoromethanesulfonyl) imide anion studied by raman spectroscopy and DFT calculations. J Phys Chem B 2007;111:13028-32.
40. Kakibe T, Ohata T, Saito T, et al. Branched alkyl functionalization of imidazolium-based ionic liquids for lithium secondary batteries. Electrochemistry 2022;90:037006.
41. Li F, Liu J, He J, et al. Additive-assisted hydrophobic Li+-solvated structure for stabilizing dual electrode electrolyte interphases through suppressing LiPF6 hydrolysis. Angew Chem Int Ed 2022;61:e202205091.
42. Huang J, Liu J, He J, et al. Optimizing electrode/electrolyte interphases and Li-ion flux/solvation for lithium-metal batteries with qua-functional heptafluorobutyric anhydride. Angew Chem Int Ed 2021;60:20717-22.
43. Qiao L, Oteo U, Martinez-Ibañez M, et al. Stable non-corrosive sulfonimide salt for 4-V-class lithium metal batteries. Nat Mater 2022;21:455-62.
44. Zeng Z, Liu X, Jiang X, et al. Enabling an intrinsically safe and high-energy-density 4.5 V-class Li-ion battery with nonflammable electrolyte. InfoMat 2020;2:984-92.
45. Wang Y, Dong N, Liu B, Tian G, Qi S, Wu D. Self-adaptive gel poly(imide-siloxane) binder ensuring stable cathode-electrolyte interface for achieving high-performance NCM811 cathode in lithium-ion batteries. Energy Stor Mater 2023;56:621-30.
46. Kim JH, Kim H, Kim W, et al. Incorporation of titanium into Ni-rich layered cathode materials for lithium-ion batteries. ACS Appl Energy Mater 2020;3:12204-11.
47. Wang L, Su Q, Shi W, et al. Optimized structure stability and cycling performance of LiNi0.8Co0.1Mn0.1O2 through homogeneous nano-thickness Al2O3 coating. Electrochim Acta 2022;435:141411.
48. Liu Q, Yang G, Liu S, Han M, Wang Z, Chen L. Trimethyl borate as film-forming electrolyte additive to improve high-voltage performances. ACS Appl Mater Interface 2019;11:17435-43.
Cite This Article
Export citation file: BibTeX | RIS
OAE Style
Liao K, Song J, Ge J, Si J, Cai Y, Luo Z, Zhou M, Liang H, Cheng YJ, Milanovic M, Inoishi A, Okada S. Protective behavior of phosphonate-functionalized imidazolium ionic liquid and its impact on the Li-ion battery performance. Energy Mater 2023;3:300044. http://dx.doi.org/10.20517/energymater.2023.33
AMA Style
Liao K, Song J, Ge J, Si J, Cai Y, Luo Z, Zhou M, Liang H, Cheng YJ, Milanovic M, Inoishi A, Okada S. Protective behavior of phosphonate-functionalized imidazolium ionic liquid and its impact on the Li-ion battery performance. Energy Materials. 2023; 3(5): 300044. http://dx.doi.org/10.20517/energymater.2023.33
Chicago/Turabian Style
Liao, Kaisi, Jingbo Song, Jiawen Ge, Jia Si, Yinxiao Cai, Zijuan Luo, Mingjiong Zhou, Hongze Liang, Ya-Jun Cheng, Marija Milanovic, Atsushi Inoishi, Shigeto Okada. 2023. "Protective behavior of phosphonate-functionalized imidazolium ionic liquid and its impact on the Li-ion battery performance" Energy Materials. 3, no.5: 300044. http://dx.doi.org/10.20517/energymater.2023.33
ACS Style
Liao, K.; Song J.; Ge J.; Si J.; Cai Y.; Luo Z.; Zhou M.; Liang H.; Cheng Y.J.; Milanovic M.; Inoishi A.; Okada S. Protective behavior of phosphonate-functionalized imidazolium ionic liquid and its impact on the Li-ion battery performance. Energy Mater. 2023, 3, 300044. http://dx.doi.org/10.20517/energymater.2023.33
About This Article
Special Issue
Copyright
Data & Comments
Data
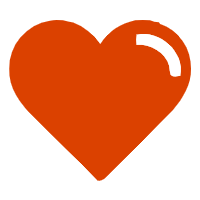

Comments
Comments must be written in English. Spam, offensive content, impersonation, and private information will not be permitted. If any comment is reported and identified as inappropriate content by OAE staff, the comment will be removed without notice. If you have any queries or need any help, please contact us at support@oaepublish.com.