High-stability room temperature ionic liquids: enabling efficient charge transfer in solid-state batteries by minimizing interfacial resistance
Abstract
Currently, intensive research is underway to develop stable electrolyte systems that can significantly enhance the performance of rechargeable batteries. Recent advances in solid electrolytes have led to new types of promising systems owing to their high conductivity. This has generated considerable interest in the practical applications of safe batteries. Considering the safety concerns associated with rechargeable batteries, solid electrolytes have become indispensable for the advancement of next-generation battery technologies. However, the increased interfacial resistance at solid-solid interfaces has become a critical challenge. To address this problem, room-temperature ionic liquids (RTILs) have been investigated as functional materials for mitigating the interfacial resistance in solid-state batteries (SSBs). The special properties of RTILs, such as their non-volatility, non-flammability, and high safety characteristics, make them highly promising candidates for safe batteries. Various approaches have been explored for the effective utilization of ionic liquids in SSBs. This review provides a comprehensive discussion on the application of RTILs as electrolytes, considering their electrochemical properties and incorporation into composites to minimize resistance in SSBs.
Keywords
INTRODUCTION
The importance of rechargeable battery systems in addressing and mitigating global issues, such as climate change and global warming, is increasing. Over the past decade, the rechargeable battery market, led by electric vehicles and large-scale energy storage systems, has experienced rapid growth. In particular, lithium-ion batteries (LIBs) have been widely used as optimal secondary battery systems for energy conversion and storage since their initial commercialization in 1991. LIBs must satisfy various performance criteria, including energy, power, cyclability, safety, cost, environmental friendliness, and temperature ranges. Considering these parameters, LIBs are the most widely utilized electrochemical energy-conversion devices and provide the highest level of performance.
With the recent emergence of numerous applications requiring kWh-to-MWh-scale secondary batteries, safety has garnered significant attention. Recently, several fire accidents involving electric vehicles and energy storage systems have been reported[1]. Considering the history of the downfall of the lithium metal battery market owing to safety concerns regarding lithium dendrite failures, addressing the safety issues of secondary batteries is one of the most critical challenges in their applications[2-4]. The key components of secondary batteries are the cathode, anode, electrolyte, and separator. For conventional LIBs, carbonate-based electrolytes are utilized to provide a robust solid electrolyte interface (SEI) on the negative electrolyte and the high solubility of lithium salts. From a safety viewpoint, carbonate-based electrolytes pose inherent challenges owing to their volatility, low flashpoints, and high flammability. However, these electrolytes offer high battery performance through excellent film formation and wetting characteristics on graphite, making it difficult to transition to safer alternative electrolytes.
Room-temperature ionic liquids (RTILs) are unique solutions that exhibit both ionic and liquid states, even at room temperature[5-8]. The distinctive characteristics of RTILs are that they are non-volatile, with negligible ignition points and flammability, making them excellent and safe electrolyte candidates for LIBs. Considering the flammability issues often associated with liquid electrolytes, RTILs have great safety potential for applications in LIBs. Although attempts have been made to use RTILs as electrolytes for lithium secondary batteries for a long time, their application has been limited because of their electrochemical reactivity, low conductivity, and corrosiveness to electrode materials[9-12].
There has been a growing interest in the development of solid electrolytes for high-safety solid-state batteries (SSBs). Solid electrolytes in batteries not only possess excellent thermal stability but also prevent the rapid spread of battery ignition by minimizing electrolyte leakage, even if the battery is damaged[13,14].
In particular, the interfacial resistance of SSBs is considerably high because of their exclusively solid interfaces, unlike routine electrochemical systems with liquid electrolytes [Figure 1][18-20]. In batteries, electrochemical reactions occur at the interfaces where ions and electrons can be transported simultaneously. Liquid electrolytes act primarily as ion conductors, whereas carbon powder and metal substrates serve as electronic conductors. Finding electrode systems that demonstrate excellent ion and electron conductivities in SSBs poses a significant challenge to achieving high-performance SSBs. The formation of ternary interfaces among the active materials, conductive carbon powder (as the electrode conducting agent), and solid electrolytes with high ionic conductivities is limited. Owing to this limitation, solid electrolytes have a less electrochemically active interface than liquid electrolytes, resulting in a high interfacial resistance[21].
Figure 1. (A) Schematic figure of all-solid batteries with active materials (cathodes and anodes), conducting agents, solid electrolytes, and ionic liquids. Enlarged particle interface among conducting agents, solid electrolytes, and active materials (B) without ionic liquids or (C) with ionic liquids.
Incorporating a small amount of RTILs as a supporting liquid electrolyte in SSBs is highly effective. The integration of a small number of nonflammable RTILs into SSBs aligns effectively with the goal of enhancing battery safety and contributing to the reinforcement of battery safety issues. The non-volatile characteristics of RTILs match the merits of SSBs. In this review, we summarize the studies on the use of RTILs in SSBs. Additionally, we discuss the phenomenological issues related to the reduction in interfacial resistance highlighted in the relevant literature and explore future directions.
ELECTROCHEMICAL STABILITY OF IONIC LIQUID
Ionic materials typically exist in the solid state at room temperature owing to the strong coulombic interactions between cations and anions. Similarly, RTILs primarily consist of cationic and anionic molecular structures, the structural stability and properties of which are generally determined by large structures to delocalize Coulombic interactions. These bulky ionic molecular structures allow the introduction of various substituents, so they are frequently referred to as designer solvents with various characteristics. Various forms of RTILs combining different types of cations and anions have been proposed. Suitable electrolytes for electrochemical systems and rechargeable batteries need to possess essential electrochemical properties such as high electrochemical stability and ionic conductivity. In the early stages of RTILs, aluminum-chloride-based ions were used as anion sources; however, they exhibited poor moisture stability and high metal corrosiveness, making them unsuitable as electrolytes for secondary batteries[22,23]. As shown in Figure 2, the RTILs were prepared with bulky anions, which are the same as the lithium salts in the liquid electrolytes used for LIBs. Imidazolium, pyrrolidinium, piperidinium, and quaternary ammonium are used as cations, whereas anions, such as TFSI and FSI, from the fluorinated series are utilized[24-27]. Depending on the binding affinity between the cations and anions, there are cases where they exist as liquids at room temperature and cases where they do not exist. The design of the cation and anion structures is aimed at reducing mutual Coulombic interactions by controlling the substituents. Electrolytes that dissolve lithium salts in glyme-based solvents are also categorized as ionic liquids because of their low volatility and low flammability[28-30].
Figure 2. (A) Physical characteristics of ionic liquids. (B) Representative cation and anion structures for ionic liquids.
In LIBs, high-voltage cathode and low-voltage anode materials are used to achieve high energy densities. The general requirement for electrolytes in electrochemical systems is that they remain inert and do not participate in the electrochemical reactions. In some cases, such as in redox flow batteries, the electrolyte may participate in electrochemical reactions; however, this is an exceptional case. Therefore, for the stable operation of secondary batteries, the electrochemical stability of RTILs should encompass the operating voltage ranges of both the cathode and anode. The electrochemical potential window is determined by the HOMO/LUMO energy levels of the RTILs[31-33]. Generally, the oxidative stability of ionic liquids is determined by the choice of anion, whereas the reductive stability is influenced by the cation. Recent studies have reported that the interplay between cations and anions can also affect electrochemical stability[31].
However, even if the HOMO/LUMO levels of the electrolyte do not meet the voltage window of the battery, SEIs can stop unwanted reactions in the electrolyte. The performance of batteries can vary depending on the combination of the electrode and electrolyte; therefore, both the electrochemical stability and the electrode film formation mechanism need to be considered simultaneously. M. Ishikawa reported that when using an electrolyte based on 1-ethyl-3-methylimidazolium (EMIm+), in combination with lithium salts, in the presence of BF4- anions in TFSI-, FSI-, and BF4- combinations, the BF4- anions formed an unstable SEI on the lithium metal surface, while anions, such as FSI- and TFSI-, were reported to form stable SEI on the lithium metal[34,35]. The SEIs from FSI- and TFSI- effectively reduced the electrochemical reduction deposition of EMIm+ on RTILs. Thus, the SEI film on the negative electrode was highly influenced by the anionic species of the RTILs. Some chemical species, such as vinyl carbonates (VC), fluoroethylene carbonates (FEC), and vinylethylene carbonates (VEC), have been used to protect the anode by forming a stable SEI[36-38]. These additives can also be used to stabilize RTILs on negative electrodes[39-41].
For the cathode, the cation substituents were controlled to deliver a cathode-electrolyte interface (CEI). The long alkyl, allyl, and cyano groups were substituted with imidazolium, pyrrolidinium, and piperidinium to improve the CEI of the positive electrode and the electrochemical stability[24,34,42,43]. Previous SEI analyses confirmed the presence of fluoride and organic films, indicating that both RTIL ions contributed to the formation of the SEI.
IONIC CONDUCTIVITY OF IONIC LIQUID
Ionic liquids are ionic materials that exhibit both ionic conductivity and solvent properties. However, lithium-ion conductivity is required for lithium secondary batteries, which distinguishes them from the conductivity of typical RTILs. Lithium salts, which contain the same anions as RTILs, are commonly used in combination with RTILs. In cases where different anions are used, they may not exist as liquids, depending on the type of RTIL used. Generally, RTILs containing imidazolium salts exhibit low viscosity and good ion conductivity[31,44,45]. They can be liquids even with BF4-, which has smaller anions than TFSI- and FSI-. However, imidazolium with FSI- and TFSI- exhibited lower viscosities and higher conductivities than those with BF4-. EMIm+ with TFSI- and FSI- demonstrates the lowest level of viscosity and the highest level of conductivity (EMI-TFSI: η = 34, σ = 14.4 mS cm-2 & EMI-FSI: η = 18, σ= 15.4 mS cm-2,
Viscosity and ionic conductivity with various structured RTILs
Cation | Substituent1 | Substituent2 | Anion | Viscosity (cP) | Conductivity (mS/cm) | Ref. |
Imidazolium | Ethyl | Methyl | BF4- | 27 | 14.4 | [46] |
Propyl | Methyl | BF4- | 58 | 7.2 | [46] | |
Butyl | Methyl | BF4- | 76 | 4.3 | [46] | |
Isobutyl | Methyl | BF4- | 76 | 1.8 | [46] | |
Allyl | Methyl | BF4- | 45 | 10.0 | [46] | |
Ethyl | Methyl | TFSI- | 34 | 8.6 | [49,50] | |
Butyl | Methyl | TFSI- | 52 | 3.9 | [50,51] | |
Ethyl | Methyl | FSI- | 18 | 15.4 | [47] | |
Pyrrolidinium | Propyl | Methyl | TFSI- | 59 | 4.9 | [47] |
Allyl | Methyl | TFSI- | 52 | 5.7 | [47] | |
Allyl | Allyl | TFSI- | 57 | 4.6 | [47] | |
Propyl | Methyl | FSI- | 40 | 8.2 | [47] | |
Piperidinium | Propyl | Methyl | TFSI- | 141 | 2.9 | [47] |
Allyl | Methyl | TFSI- | 108 | 3.5 | [47] | |
Allyl | Allyl | TFSI- | 113 | 2.3 | [47] | |
Propyl | Methyl | FSI- | 95 | 3.7 | [47] | |
Ammonium | isobutyl | Methyl | TFSI- | 100 | 0.017 | [51] |
isobutyl | Methyl | FSI- | 53 | 5.8 | [51] | |
Allyl | Ethyl | TFSI- | 67 | 2.5 | [48] | |
Allyl | Propyl | TFSI- | 79 | 2.1 | [48] |
However, the use of imidazolium salts as RTIL electrolytes is limited because of their poor electrochemical stability. The presence of an acidic proton at the imidazolium 2-C position leads to poor electrochemical reduction stability. To overcome this problem, RTILs that incorporate cyclic or quaternary ammonium cations have been introduced. These compounds include pyrrolidinium, piperidinium, and ammonium. However, these structures lack conjugation within the cationic molecular framework, which results in inferior charge delocalization. Therefore, they only exist in a liquid state at room temperature when paired with bulky anions, such as TFSI and FSI, which have high charge delocalization. In addition, their conductivities and viscosities are inferior to those of imidazolium. Thus, to achieve asymmetry in the cation, one substituent attached to the nitrogen is often fixed as a methyl group, whereas the other is substituted with a relatively long substituent. However, it has been found that conductivity deteriorates when substituents larger than the propyl group are introduced. Among these alternative cations, pyrrolidinium is the most feasible cation candidate for RTILs because of its low viscosity and high conductivity (PMPyr-TFSI: η = 59, σ = 4.9 mS cm-2, as shown in Table 1).
STRATEGIES FOR MINIMIZING RESISTANCE OF BATTERIES
Sulfide-type solid electrolyte
Solid electrolytes used in SSBs can be classified as oxide- or sulfide-based. Between these two, sulfide-based solid electrolytes exhibit higher ionic conductivities than oxide-based solid electrolytes. Consequently, there has been a recent focus on research related to sulfide-based solid electrolytes[52-54]. In 2015, Jung proposed the first SSB system using RTILs with anhydrous triglyme combined with Li-TFSI as an interfacial ion transport stabilizer. This system utilized a sulfide-based solid electrolyte, LGPS, and introduced the use of an ion-conductive liquid in SSBs[55]. It has been observed that when tri-glyme is used in a molten state in the presence of lithium salts, it reduces the solubility and the reactivity of LGPS [Figure 3A]. This reduces the interfacial resistance between the LiFePO4 (LFP) cathode particles and the LGPS solid electrolyte. In 2019, the same research group reported a slurry-based SSB electrode fabrication process using nitrile butadiene rubber (NBR), a polymer, and an RTIL to control the solvation environment and achieve high interfacial conductivity[56]. Gao reported a stable cycle life of 2000 cycles at a current density of 2.5 C for a half-cell battery system utilizing LiG3-Li-TFSI RTILs with an LGPS electrolyte on a Li4Ti5O12 anode[57]. Fan improved the cyclability characteristics of LiNi0.6Co0.2Mn0.2O2 (NCM622) and Li metal batteries using a Li6PS5Cl argyrodite electrolyte, which is also a representative sulfide solid electrolyte. They applied
Figure 3. (A) Stability of tri-glyme ionic liquid electrolyte and voltage curves with/without ionic liquids[55]. (B) Voltage curves of Li-Li symmetric cells with LSPS solid electrolyte and ionic liquids[59]. (C) Cycle performance and Nyquist plot of RTIL-LiTFSI-PEO hybrid interphase material and NBR binder[61].
Yang reported the physical/chemical improvements of 1.5 M LiTFSI/N-propyl-N-methylpyrrolidinium (PMPyr) TFSI electrolyte on the lithium surface of the sulfide-based solid electrolyte Li10SnP2S12. This study demonstrated a reduction in the lithium surface resistance, indicating improved performance in terms of physical and chemical properties [Figure 3B][59]. Cho utilized a solid electrolyte with minimal ionic liquid content on the surface of LGPS by separating the LGPS material from the N-butyl-N-methylpyrrolidinium (BMPyr) TFSI electrolyte after stirring. The study reported that LGPS exhibits high stability in pyrrolidinium-based electrolytes and reduces contact resistance, resulting in decreased solid electrode contact resistance in LiNi0.8Co0.1Mn0.1O2 (NCM811) high-voltage, high-capacity cathode materials[60]. A subsequent study reported a cyclability of 50 cycles, achieving performance comparable to that of high-pressure coin cells through the manufacturing method of NCM cathodes coated with polyethylene oxide (PEO) material and its composites in the form of slurry coating on LGPS solid-state electrolyte pellets
Oxide-type solid electrolyte
There are many reports on the combination of oxide-type solid electrolytes and RTILs. Oxide-type solid electrolytes have more severe interfacial resistance problems owing to their lower conductivity than sulfide-type solid electrolytes. In addition, when pressure is applied to sulfide-based solid electrolytes, a relatively ductile interface is formed, resulting in a wide interface. However, it is difficult for solid oxides to form such wide interfaces, even under high pressure. In contrast, oxide-type solid electrolytes exhibit a wide electrochemical stability window[65]. In this regard, RTILs are expected to mitigate the increase in resistance caused by subreactions at the oxide electrolyte interface. Owing to the rigid, solid nature of oxide electrolytes, the increased contact obtained from the lower interfacial resistance resulting from the formation of a liquid interface is expected to have a more significant effect. Traditionally, ceramic materials, such as Al2O3 or SiO2, have been used as supports for gel polymer composites that combine polymers such as PVDF and RTILs[66-69]. It is known that the metal oxide surface aids in lithium-ion transport, leading to improved conductivity, and the combination of oxides with RTILs is a well-established research approach. In other words, the combination of metal oxides results in increased conductivity and enhanced mechanical strength, which has long been reported. However, with the increasing conductivity of oxide-type solid electrolytes, there has been a greater focus on the role of RTILs as enhancers of the physical electrode interface conductivity rather than solely improving the electrolyte conductivity.
Kohl reported the use of LISICON and 1.0 M Li-TFSI PMPyr-FSI as separator replacement materials for the stable operation of graphite/Li metal half-cell batteries even at high temperatures [Figure 4A][70]. Previously, it was reported that a PMPyr-FSI liquid electrolyte can form a stable SEI on both lithium metal and graphite electrodes in conventional LIBs[71-73]. It has been found that the same type of FSI electrolyte can also form a stable SEI in such solid-type systems. Various high-conductivity oxide-based solid electrolytes, such as
Figure 4. (A) Schematic figure of a LISCON separator half-cell with wetting agent[70]. (B) Voltage curves of Li-Li symmetric cell with LLZO and ionic liquids[79]. (C) Schematic figures of LLZO and ionic liquid electrolyte in SSBs and cross-sectional SEM images representing interfacial failure modes[85]. (D) (Left) Schematic figure of the flexible composite Al-LLZO sheet and its fabrication procedure. (Right) Voltage curves from LiCoO2 half-cells at 30 °C[86].
In addition to simply mixing RTILs and oxide electrolytes, research has also reported the enhancement of interfacial safety using LATP oxide solid electrolytes in combination with PMPyr-TFSI and poly
PERSPECTIVE & OUTLOOK
All-solid-state batteries, which do not have a conventional electrochemical liquid interface between the electrodes and electrolyte, generally suffer from high interfacial resistance. More critically, degradation at the electrode-SEI in all-solid-state batteries has been identified as a major factor that exacerbates the interfacial resistance. Under such circumstances, RTILs, which can form a liquid interface, have the potential to be applied in the manufacturing process of all-solid-state batteries without compromising safety owing to their non-volatility and electrochemical/chemical stability. Research on RTILs as ion-conductive media has been consistently conducted, building upon knowledge gained, particularly for LIBs with many combinations of active materials[4,10,87-89]. Many RTIL/solid electrolyte composite results have been reported, and it is anticipated that interface stabilization through RTILs will continue to gain attention as they contribute to enhancing the completeness of all-solid-state batteries.
The development of novel RTILs that ensure interfacial stability with sulfide- and oxide-type solid electrolytes, along with the introduction of a new all-solid-state battery system, is expected to be a highly promising approach. Sulfide-based battery systems have been the subject of numerous studies owing to their high conductivity, which makes them suitable for all-solid-state battery systems. This is because the high conductivity of the solid electrolyte enables more promising technological development towards all-solid-state batteries by reducing the contact resistance via highly conductive and safe RTILs contained within. However, developing new RTILs that are electrochemically and chemically stable in fragile sulfide-type solid electrolytes is necessary. New types of RTILs that lead to the stable passivation of electrode-active materials can be pursued. Additionally, the development of stable and conducting RTIL electrolytes capable of compensating for high interfacial resistance can serve as an approach to reducing solid/solid interfacial resistance [Figure 5].
Figure 5. Schematic figure of interface among active materials/solid electrolyte/RTILs along electrochemical behaviors of RTILs.
In contrast, oxide-based systems have relatively low conductivities but exhibit high chemical stability. Thus, the application of RTILs in oxide systems is expected to be relatively feasible. Owing to the low electrolyte conductivity of oxide-type solid electrolytes, the use of RTILs is anticipated to be more prevalent to compensate for poor ion conductivity. In addition to reducing the interfacial contact resistance, it is expected that research on various electrode chemical interfaces will lead to the development of more complete oxide-RTIL electrolyte systems in the future. Additionally, because the liquid interface is introduced as an additional ion transport medium in all-solid-state batteries, it is expected that issues related to the viscosity and conductivity of RTILs will receive less attention than stability concerns. Once the polarization issues at the solid interface are addressed through novel RTILs, further attention must be paid to addressing the subsequent minor issues that are intricately involved in battery operation. These secondary issues include the corrosiveness, wide operating temperature range, and flammability of the RTILs. In addition to the RTILs used in conventional LIBs, new RTIL systems suitable for all-solid-state batteries are being actively investigated.
DECLARATIONS
Authors’ contributions
Proposed the topic of this review: Mun J
Prepared the manuscript: Jeong S, Ho VC, Kwon O, Park Y, Mun J
Collectively discussed and revised the manuscript: Jeong S, Ho VC, Kwon O, Park Y, Mun J
Availability of data and materials
Not applicable.
Financial support and sponsorship
This research was financially supported by the Institute of Civil Military Technology Cooperation, funded by the Defense Acquisition Program Administration, and the Ministry of Trade, Industry and Energy of the Korean government under grant No. UM22213RD2.
Conflicts of interest
All authors declared that there are no conflicts of interest.
Ethical approval and consent to participate
Not applicable.
Consent for publication
Not applicable.
Copyright
© The Author(s) 2023.
REFERENCES
1. Gao W, Li X, Ma M, Fu Y, Jiang J, Mi C. Case study of an electric vehicle battery thermal runaway and online internal short-circuit detection. IEEE Trans Power Electron 2021;36:2452-5.
2. Liao C, Han L, Wang W, et al. Non-flammable electrolyte with lithium nitrate as the only lithium salt for boosting ultra-stable cycling and fire-safety lithium metal batteries. Adv Funct Mater 2023;33:2212605.
3. Cho SJ, Yu DE, Pollard TP, et al. Nonflammable lithium metal full cells with ultra-high energy density based on coordinated carbonate electrolytes. iScience 2020;23:100844.
4. Kim HT, Kang J, Mun J, Oh SM, Yim T, Kim YG. Pyrrolinium-based ionic liquid as a flame retardant for binary electrolytes of lithium ion batteries. ACS Sustainable Chem Eng 2016;4:497-505.
6. Nakagawa H, Fujino Y, Kozono S, et al. Application of nonflammable electrolyte with room temperature ionic liquids (RTILs) for lithium-ion cells. J Power Sources 2007;174:1021-6.
7. Tang X, Lv S, Jiang K, Zhou G, Liu X. Recent development of ionic liquid-based electrolytes in lithium-ion batteries. J Power Sources 2022;542:231792.
8. Watanabe M, Thomas ML, Zhang S, Ueno K, Yasuda T, Dokko K. Application of ionic liquids to energy storage and conversion materials and devices. Chem Rev 2017;117:7190-239.
9. Seong MJ, Yim T. Ionic additives to increase electrochemical utilization of sulfur cathode for Li-S batteries. J Electrochem Sci Technol 2021;12:279-84.
10. Yim T, Kwon MS, Mun J, Lee KT. Room temperature ionic liquid-based electrolytes as an alternative to carbonate-based electrolytes. Isr J Chem 2015;55:586-98.
11. Mun J, Yim T, Choi CY, Ryu JH, Kim YG, Oh SM. Linear-sweep thermammetry study on corrosion behavior of Al current collector in ionic liquid solvent. Electrochem Solid-State Lett 2010;13:A109.
12. Cha EH, Mun JY, Cho ER, et al. The corrosion study of Al current collector in phosphonium ionic liquid as solvent for lithium ion battery. J Korean Electrochem Soc 2011;14:152-6.
13. Heo K, Im J, Lee JS, et al. High-rate blended cathode with mixed morphology for all-solid-state Li-ion batteries. J Electrochem Sci Technol 2020;11:282-90.
14. Murali A, Sakar M, Priya S, et al. Insights into the emerging alternative polymer-based electrolytes for all solid-state lithium-ion batteries: a review. Mater Lett 2022;313:131764.
16. Liu X, Zheng B, Zhao J, et al. Electrochemo-mechanical effects on structural integrity of ni-rich cathodes with different microstructures in all solid-state batteries. Adv Energy Mater 2021;11:2003583.
17. Paul PP, Chen BR, Langevin SA, Dufek EJ, Nelson Weker J, Ko JS. Interfaces in all solid state Li-metal batteries: a review on instabilities, stabilization strategies, and scalability. Energy Stor Mater 2022;45:969-1001.
18. Yoon K, Kim JJ, Seong WM, Lee MH, Kang K. Investigation on the interface between Li10GeP2S12 electrolyte and carbon conductive agents in all-solid-state lithium battery. Sci Rep 2018;8:8066.
19. Kato T, Yoshida R, Yamamoto K, et al. Effects of sintering temperature on interfacial structure and interfacial resistance for all-solid-state rechargeable lithium batteries. J Power Sources 2016;325:584-90.
20. Ohta S, Kobayashi T, Seki J, Asaoka T. Electrochemical performance of an all-solid-state lithium ion battery with garnet-type oxide electrolyte. J Power Sources 2012;202:332-5.
21. Abe T, Sagane F, Ohtsuka M, Iriyama Y, Ogumi Z. Lithium-Ion transfer at the interface between lithium-ion conductive ceramic electrolyte and liquid electrolyte-a key to enhancing the rate capability of lithium-ion batteries. J Electrochem Soc 2005;152:A2151.
22. Wang Q, Chen B, Zhang Q, Lu X, Zhang S. Aluminum deposition from lewis acidic 1-butyl-3-methylimidazolium chloroaluminate ionic liquid ([Bmim Cl/AlCl3]) modified with methyl nicotinate. ChemElectroChem 2015;2:1794-8.
24. Mun J, Kim S, Yim T, Ryu JH, Kim YG, Oh SM. Comparative study on surface films from ionic liquids containing saturated and unsaturated substituent for LiCoO2. J Electrochem Soc 2010;157:A136.
25. Mun J, Yim T, Park K, Ryu JH, Kim YG, Oh SM. Surface film formation on LiNi0.5Mn1.5O4 electrode in an ionic liquid solvent at elevated temperature. J Electrochem Soc 2011;158:A453.
26. Cho E, Mun J, Chae OB, et al. Corrosion/passivation of aluminum current collector in bis(fluorosulfonyl)imide-based ionic liquid for lithium-ion batteries. Electrochem Commun 2012;22:1-3.
27. Chakrapani V, Rusli F, Filler MA, Kohl PA. Quaternary ammonium ionic liquid electrolyte for a silicon nanowire-based lithium ion battery. J Phys Chem C 2011;115:22048-53.
28. Tobishima S, Morimoto H, Aoki M, et al. Glyme-based nonaqueous electrolytes for rechargeable lithium cells. Electrochim Acta 2004;49:979-87.
29. Carbone L, Di Lecce D, Gobet M, et al. Relevant features of a triethylene glycol dimethyl ether-based electrolyte for application in lithium battery. ACS Appl Mater Interfaces 2017;9:17085-95.
30. Carbone L, Gobet M, Peng J, et al. Comparative study of ether-based electrolytes for application in lithium-sulfur battery. ACS Appl Mater Interfaces 2015;7:13859-65.
31. Kazemiabnavi S, Zhang Z, Thornton K, Banerjee S. Electrochemical stability window of imidazolium-based ionic liquids as electrolytes for lithium batteries. J Phys Chem B 2016;120:5691-702.
32. De vos N, Maton C, Stevens CV. Electrochemical stability of ionic liquids: general influences and degradation mechanisms. Chemelectroche 2014;1:1258-70.
33. Zhao C, Burrell G, Torriero AA, et al. Electrochemistry of room temperature protic ionic liquids. J Phys Chem B 2008;112:6923-36.
34. Zhao L, Yamaki J, Egashira M. Analysis of SEI formed with cyano-containing imidazolium-based ionic liquid electrolyte in lithium secondary batteries. J Power Sources 2007;174:352-8.
35. Sugimoto T, Atsumi Y, Kikuta M, Ishiko E, Kono M, Ishikawa M. Ionic liquid electrolyte systems based on bis(fluorosulfonyl)imide for lithium-ion batteries. J Power Sources 2009;189:802-5.
36. An Y, Zuo P, Du C, et al. Effects of VC-LiBOB binary additives on SEI formation in ionic liquid-organic composite electrolyte. RSC Adv 2012;2:4097-102.
37. El Ouatani L, Dedryvère R, Siret C, et al. The effect of vinylene carbonate additive on surface film formation on both electrodes in li-ion batteries. J Electrochem Soc 2009;156:A103.
38. Choi NS, Yew KH, Lee KY, Sung M, Kim H, Kim SS. Effect of fluoroethylene carbonate additive on interfacial properties of silicon thin-film electrode. J Power Sources 2006;161:1254-9.
39. Lewandowski A, Świderska-mocek A. Properties of the lithium and graphite-lithium anodes in N-methyl-N-propylpyrrolidinium bis(trifluoromethanesulfonyl)imide. J Power Sources 2009;194:502-7.
40. Fu Y, Chen C, Qiu C, Ma X. Vinyl ethylene carbonate as an additive to ionic liquid electrolyte for lithium ion batteries. J Appl Electrochem 2009;39:2597-603.
41. Sano H, Sakaebe H, Matsumoto H. Effect of organic additives on electrochemical properties of Li anode in room temperature ionic liquid. J Electrochem Soc 2011;158:A316.
42. Seki S, Mita Y, Tokuda H, et al. Effects of alkyl chain in imidazolium-type room-temperature ionic liquids as lithium secondary battery electrolytes. Electrochem Solid-State Lett 2007;10:A237.
43. Mun J, Yim T, Park JH, et al. Allylic ionic liquid electrolyte-assisted electrochemical surface passivation of LiCoO2 for advanced, safe lithium-ion batteries. Sci Rep 2014;4:5802.
44. Hofmann A, Migeot M, Arens L, Hanemann T. Investigation of ternary mixtures containing 1-ethyl-3-methylimidazolium bis(trifluoromethanesulfonyl)azanide, ethylene carbonate and lithium bis(trifluoromethanesulfonyl)azanide. Int J Mol Sci 2016;17:670.
45. Kruusma J, Tõnisoo A, Pärna R, et al. The electrochemical behavior of 1-ethyl-3-methyl imidazolium tetracyanoborate visualized by in situ X-ray photoelectron spectroscopy at the negatively and positively polarized micro-mesoporous carbon electrode. J Electrochem Soc 2017;164:A3393-402.
46. Min GH, Yim T, Lee HY, et al. Synthesis and properties of ionic liquids:imidazolium tetrafluoroborates with unsaturated side chains. Bull Korean Chem Soc 2006;27:847-52.
47. Yim TE, Lee HY, Kim HJ, et al. Synthesis and properties of pyrrolidinium and piperidinium bis(trifluoromethanesulfonyl)imide ionic liquids with allyl substituents. Bull Korean Chem Soc 2007;28:1567-72.
48. Yim T, Choi CY, Mun J, Oh SM, Kim YG. Synthesis and properties of acyclic ammonium-based ionic liquids with allyl substituents as electrolytes. Molecules 2009;14:1840-51.
49. Nanjundiah C, Mcdevitt SF, Koch VR. Differential capacitance measurements in solvent-free ionic liquids at Hg and C interfaces. J Electrochem Soc 1997;144:3392-7.
50. Furuya R, Tachikawa N, Yoshii K, Katayama Y, Miura T. Deposition and dissolution of lithium through lithium phosphorus oxynitride thin film in some ionic liquids. J Electrochem Soc 2015;162:H634-7.
51. Furuya R, Katayama Y, Miura T. Deposition and dissolution of lithium through lithium phosphorus oxynitride thin film in some ionic liquids. ECS Trans 2014;64:453-9.
52. Zuo TT, Walther F, Ahmed S, et al. Formation of an artificial cathode-electrolyte interphase to suppress interfacial degradation of Ni-rich cathode active material with sulfide electrolytes for solid-state batteries. ACS Energy Lett 2023;8:1322-9.
53. Liu X, Cheng Y, Su Y, et al. Revealing the surface-to-bulk degradation mechanism of nickel-rich cathode in sulfide all-solid-state batteries. Energy Stor Mater 2023;54:713-23.
54. Kim KT, Kwon TY, Song YB, et al. Wet-slurry fabrication using PVdF-HFP binder with sulfide electrolytes via synergetic cosolvent approach for all-solid-state batteries. Chem Eng J 2022;450:138047.
55. Oh DY, Nam YJ, Park KH, et al. Excellent compatibility of solvate ionic liquids with sulfide solid electrolytes: toward favorable ionic contacts in bulk-type all-solid-state lithium-ion batteries. Adv Energy Mater 2015;5:1500865.
56. Oh DY, Nam YJ, Park KH, et al. Slurry-fabricable Li+-conductive polymeric binders for practical all-solid-state lithium-ion batteries enabled by solvate ionic liquids. Adv Energy Mater 2019;9:1802927.
57. Cao Y, Lou S, Sun Z, et al. Solvate ionic liquid boosting favorable interfaces kinetics to achieve the excellent performance of Li4Ti5O12 anodes in Li10GeP2S12 based solid-state batteries. Chem Eng J 2020;382:123046.
58. Yi J, Yan C, Zhou D, Fan L. A robust solid electrolyte interphase enabled by solvate ionic liquid for high-performance sulfide-based all-solid-state lithium metal batteries. Nano Res 2023;16:8411-6.
59. Zheng B, Zhu J, Wang H, et al. Stabilizing Li10SnP2S12/Li interface via an in Situ formed solid electrolyte interphase layer. ACS Appl Mater Interfaces 2018;10:25473-82.
60. Kim K, Park J, Jeong G, et al. Rational design of a composite electrode to realize a high-performance all-solid-state battery. ChemSusChem 2019;12:2637-43.
61. Cho W, Park J, Kim K, Yu JS, Jeong G. Sulfide-compatible conductive and adhesive glue-like interphase engineering for sheet-type all-solid-state battery. Small 2021;17:e1902138.
62. Wang Z, Zhang L, Shang X, et al. Enhanced electrochemical performance enabled by ionic-liquid-coated Na3SbS4 electrolyte encapsulated in flexible filtration membrane. Chem Eng J 2022;428:132094.
63. Li Y, Halacoglu S, Shreyas V, et al. Highly efficient interface stabilization for ambient-temperature quasi-solid-state sodium metal batteries. Chem Eng J 2022;434:134679.
64. An T, Jia H, Peng L, Xie J. Material and interfacial modification toward a stable room-temperature solid-state Na-S battery. ACS Appl Mater Interfaces 2020;12:20563-9.
65. Tao B, Ren C, Li H, et al. Thio-/LISICON and LGPS-type solid electrolytes for all-solid-state lithium-ion batteries. Adv Funct Materials 2022;32:2203551.
66. Zhang X, Wang S, Xue C, et al. Self-suppression of lithium dendrite in all-solid-state lithium metal batteries with poly(vinylidene difluoride)-based solid electrolytes. Adv Mater 2019;31:e1806082.
67. Fuller J, Breda AC, Carlin RT. Ionic liquid-polymer gel electrolytes from hydrophilic and hydrophobic ionic liquids. J Electroanal Chem 1998;459:29-34.
68. Fuller J, Breda AC, Carlin RT. Ionic liquid-polymer gel electrolytes. J Electrochem Soc 1997;144:L67.
69. Hashmi SA, Bhat MY, Singh MK, Sundaram NTK, Raghupathy BPC, Tanaka H. Ionic liquid-based sodium ion-conducting composite gel polymer electrolytes: effect of active and passive fillers. J Solid State Electrochem 2016;20:2817-26.
70. Kim H, Ding Y, Kohl PA. LiSICON - ionic liquid electrolyte for lithium ion battery. J Power Sources 2012;198:281-6.
71. Matsumoto H, Sakaebe H, Tatsumi K, Kikuta M, Ishiko E, Kono M. Fast cycling of Li/LiCoO2 cell with low-viscosity ionic liquids based on bis(fluorosulfonyl)imide [FSI]-. J Power Sources 2006;160:1308-13.
72. Guerfi A, Duchesne S, Kobayashi Y, Vijh A, Zaghib K. LiFePO4 and graphite electrodes with ionic liquids based on bis(fluorosulfonyl)imide (FSI)- for Li-ion batteries. J Power Sources 2008;175:866-73.
73. Sugimoto T, Kikuta M, Ishiko E, Kono M, Ishikawa M. Ionic liquid electrolytes compatible with graphitized carbon negative without additive and their effects on interfacial properties. J Power Sources 2008;183:436-40.
74. Murugan R, Thangadurai V, Weppner W. Fast lithium ion conduction in garnet-type Li7La3Zr2O12. Angew Chem Int Ed Eng 2007;46:7778-81.
75. Zhu Y, He X, Mo Y. Origin of Outstanding Stability in the Lithium Solid Electrolyte Materials: Insights from Thermodynamic Analyses Based on First-Principles Calculations. ACS Appl Mater Interfaces 2015;7:23685-93.
76. Teranishi T, Ishii Y, Hayashi H, Kishimoto A. Lithium ion conductivity of oriented Li0.33La0.56TiO3 solid electrolyte films prepared by a sol-gel process. Solid State Ionics 2016;284:1-6.
77. Sugata S, Saito N, Watanabe A, et al. Quasi-solid-state lithium batteries using bulk-size transparent Li7La3Zr2O12 electrolytes. Solid State Ion 2018;319:285-90.
78. Xiong S, Liu Y, Jankowski P, et al. Design of a multifunctional interlayer for NASCION-based solid-state Li metal batteries. Adv Funct Mater 2020;30:2001444.
79. Pervez SA, Kim G, Vinayan BP, et al. Overcoming the interfacial limitations imposed by the solid-solid interface in solid-state batteries using ionic liquid-based interlayers. Small 2020;16:e2000279.
80. Chen Z, Gao X, Kim JK, Kim GT, Passerini S. Quasi-solid-state lithium metal batteries using the LiNi0.8Co0.1Mn0.1O2-Li1+ xAlxTi2-x
81. Song X, Wang C, Chen J, et al. Unraveling the synergistic coupling mechanism of Li+ transport in an “ionogel-in-ceramic” hybrid solid electrolyte for rechargeable lithium metal battery. Adv Funct Mater 2022;32:2108706.
82. Song X, Zhang H, Jiang D, et al. Enhanced transport and favorable distribution of Li-ion in a poly(ionic liquid) based electrolyte facilitated by Li1.3Al0.3Ti1.7(PO4)3 nanoparticles for highly-safe lithium metal batteries. Electrochim Acta 2021;368:137581.
83. Liu Z, Borodin A, Endres F. Ionic liquid and polymer coated garnet solid electrolytes for high-energy solid-state lithium metal batteries. Energy Tech 2022;10:2270023.
84. Yu D, Ma Z, Liu Z, et al. Optimizing interfacial wetting by ionic liquid for high performance solid-state lithium metal batteries operated at ambient temperature. Chem Eng J 2023;457:141043.
85. Fuchs T, Mogwitz B, Otto SK, Passerini S, Richter FH, Janek J. Working principle of an ionic liquid interlayer during pressureless lithium stripping on Li6.25Al0.25La3Zr2O12(LLZO) garnet-type solid electrolyte. Batter Supercaps 2021;4:1145-55.
86. Cheng EJ, Kimura T, Shoji M, Ueda H, Munakata H, Kanamura K. Ceramic-based flexible sheet electrolyte for Li batteries. ACS Appl Mater Interfaces 2020;12:10382-8.
87. Yoon H, Howlett PC, Best AS, Forsyth M, Macfarlane DR. Fast charge/discharge of Li metal batteries using an ionic liquid electrolyte. J Electrochem Soc 2013;160:A1629-37.
88. Ochel A, Di Lecce D, Wolff C, Kim G, Carvalho DV, Passerini S. Physicochemical and electrochemical investigations of the ionic liquid N-butyl -N-methyl-pyrrolidinium 4,5-dicyano-2-(trifluoromethyl)imidazole. Electrochim Acta 2017;232:586-95.
Cite This Article
Export citation file: BibTeX | RIS
OAE Style
Jeong S, Ho VC, Kwon O, Park Y, Mun J. High-stability room temperature ionic liquids: enabling efficient charge transfer in solid-state batteries by minimizing interfacial resistance. Energy Mater 2023;3:300048. http://dx.doi.org/10.20517/energymater.2023.47
AMA Style
Jeong S, Ho VC, Kwon O, Park Y, Mun J. High-stability room temperature ionic liquids: enabling efficient charge transfer in solid-state batteries by minimizing interfacial resistance. Energy Materials. 2023; 3(6): 300048. http://dx.doi.org/10.20517/energymater.2023.47
Chicago/Turabian Style
Jeong, Seonghun, Van-Chuong Ho, Ohmin Kwon, Yuwon Park, Junyoung Mun. 2023. "High-stability room temperature ionic liquids: enabling efficient charge transfer in solid-state batteries by minimizing interfacial resistance" Energy Materials. 3, no.6: 300048. http://dx.doi.org/10.20517/energymater.2023.47
ACS Style
Jeong, S.; Ho V.C.; Kwon O.; Park Y.; Mun J. High-stability room temperature ionic liquids: enabling efficient charge transfer in solid-state batteries by minimizing interfacial resistance. Energy Mater. 2023, 3, 300048. http://dx.doi.org/10.20517/energymater.2023.47
About This Article
Special Issue
Copyright
Data & Comments
Data
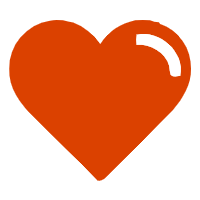

Comments
Comments must be written in English. Spam, offensive content, impersonation, and private information will not be permitted. If any comment is reported and identified as inappropriate content by OAE staff, the comment will be removed without notice. If you have any queries or need any help, please contact us at support@oaepublish.com.