Two-dimensional (2D) materials for 3D printed micro-supercapacitors and micro-batteries
Abstract
Two-dimensional (2D) materials display a unique set of physical/chemical properties and are considered potential building blocks for the manufacturing of microstructured materials for a number of applications. Prominent applications range from advanced electronics to miniaturized electrochemical energy storage devices (EESDs). Herein, we present a comprehensive and critical review of the recent developments in design and microfabrication of 2D-driven microscale electrodes for three-dimensional (3D)-printed micro-supercapacitors and micro-batteries. Firstly, we systematically discuss the advantages and disadvantages associated with various microfabrication techniques such as stereolithography, fused deposition modeling, inkjet printing, and direct ink writing. Next, key parameters disclosing the relationship between the characteristics of 2D-based materials and extrusion-driven 3D printing process for the development of versatile and sustainable EESDs are highlighted. 2D materials utilized for the construction of microelectrodes for supercapacitors (e.g., electric double layer capacitors (EDLCs), pseudocapacitors, and hybrid capacitors) and batteries (e.g., Li-based systems and next-generation systems,
Keywords
INTRODUCTION
The advent of wearable, integratable, and multifunctional microelectronics has urged the robust manufacturing of compatible microscale electrochemical energy storage devices (MEESDs) such as micro-supercapacitors (MSCs) and micro-batteries (MBs)[1-4]. The key application areas of MEESDs are
In comparison to traditional reported techniques, 3D printing technology, i.e., additive manufacturing (AM) process, which is an advanced bottom-up manufacturing technology possessing capability of developing geometrically intricate architectures with minimum operational costs and marginal wastage of materials as well[44-46]. For 3D printing of microelectrodes, the printable inks based on electroactive materials are prepared, which can be printed as per defined electrode and cell designs including shapes, sizes, and architectures and finally are packaged with electrolyte filling. In detail, 3D-printed MEESDs could have the following unique characteristics; (A) they offer design freedom at the micron-sized dimensions, with the choice to develop any required shapes owing to the ability to develop complex architectures; (B) high areal and specific capacity values along with commendable ED/PD contributions owing to maximum areal loadings (up to 14 mg cm-2) of electroactive materials and maximized aspect ratio of the 3D-structured electrodes; (C) high ED/PD owing to the minimized ions/electrons diffusion channels facilitated by the 3D architectures of the printed electrodes; and (D) lower manufacturing cost compared to other manufacturing techniques, as 3D printing can drastically reduce wastage of materials with ultimate saving potential production time and also facilitate the direct integration of MSCs and MBs with microelectronics by eliminating assembly and packaging steps[47-49].
With the subsequent development and adoption of new 3D printing techniques such as stereolithography (SLA), fused deposition modeling (FDM), direct ink writing (DIW), and inkjet printing (IJP), the assembly of 2D materials has been greatly diversified by providing more control for scalable fabrication of uniform microelectrodes and new directions for the development of 2D materials-based microstructures with required design/pattern and size[50-53]. Thus, 3D printing techniques are expanding the application range of 2D materials-based MSCs and MBs by enhancing their performance and assisting the fast growth of sustainable MEESDs. This review report aims to cover in detail the key scientific/technical points and recent trends related to 2D materials to promote high-rated 3D-printed MEESDs, e.g., MSCs and MBs. It starts with an important introduction about the well-known 3D printing techniques (e.g., DIW, FDM, IJP, and SLA), mentioning their working mechanism, materials suitability, operation procedures, advantages, and deficiencies. In the subsequent section, we have summarized the crucial roles of 2D materials-based inks in the development of sustainable 3D-printed microelectrodes. In brief, these inks can improve controllability and tailorability of the resulting 3D-printed microelectrodes. By combining the versatile functions and valuable properties of 2D materials, it is possible to design and fabricate microstructures with unprecedented features covering the requirements of the advanced microelectronics industry. Finally, the impacts of various 2D materials (categorized based on energy storage mechanism), recent materials composition trends, and other prominent factors on the reported electrochemical contributions of 3D-printed MEESDs are well-outlined. These pre-mentioned various aspects make this review systematic and comprehensive by disclosing the role of 3D printing process and 2D materials-based structures in the development of high-rated MEESDs such as MSCs (electric double layer capacitors (EDLCs), pseudocapacitors, and hybrid capacitors) and MBs (Li/Na, and zinc-ion batteries) [Figure 1]. Subsequently, to expedite further research opportunities and development of sustainable and high-rated 2D materials-based MEESDs, the associated challenges are well-elaborated. Finally, various prospects are also suggested to further enhance the electrochemical performance of 3D-printed EESDs, e.g., by eliminating the use of binders, improving mechanical stability by controlling the generation of residual stresses in the printed layers, mitigating irreversible reactions, and unrevealing the in-depth intrinsic electrochemical energy storage mechanisms of the respective devices.
3D PRINTING TECHNIQUES
According to the International Committee of the American Society for Testing and Materials (ASTM), 3D printing processes are classified into seven prominent types established on their manufacturing principles: (i) material jetting (e.g., aerosol jet printing and IJP); (ii) material extrusion (e.g., FDM and DIW); (iii) photopolymerization (e.g., two-photon lithography, SLA, and digital light processing); (iv) powder bed fusion (e.g., selective-laser-sintering); (v) sheet lamination (e.g., laminated object manufacturing); (vi) directed energy deposition (DED); and (vii) binder jetting (BJ)[54,55]. Various high-standard reviews have been reported on various 3D printing technologies, outlining comprehensively their characteristics and properties. On the other hand, this review focused on exploring and epitomizing four 3D-printed technologies that have been deployed to manufacture MSC and MB modules to date, including FDM, DIW, IJP, and SLA. The printing technique can be picked up rationally pivoting on processability parameters and feature size of the key product to attain the customized architecture and outcome of the MEESDs (MSC and MB modules). So, in this regard, it is a key phenomenon to understand the printing processes and properties of different techniques for further technology and material design refinement. This review report summarizes the printing principles, benefits/drawbacks associated with prementioned printing techniques, in terms of applicable materials range, ink requirements, design versatility, throughput, resolution,
Direct ink writing printing
Direct ink writing (DIW) printing is a pure example of extrusion-type deposition process, which starts with the preparation of viscoelastic ink with certain rheology characteristics and yield-stress behavior of the under-consideration raw material(s)[56-59]. The printability of the deployed ink is crucial and mainly based on the sustainable mechanical behaviors of the MSCs and MBs and the rheological characteristics of the printed inks. In typical synthesis process of DIW, the customized 3D architectures are fabricated by extruding a filament of active material via a nozzle under variable pressure, and filament is stacked continuously on the particular substrate. The nozzle has the capacity to move horizontally in a two-axis plane, and the platform can advance vertically downwards after the deposition of each new ink layer with the aid of computer-aided manufacturing (CAM) or computer-aided design (CAD) software. The
Figure 2. Schematic illustration of working principles and key characteristics of the prominent 3D printing processes for development of supercapacitors and batteries: (A-D) direct ink writing, fused deposition modeling, inkjet printing, and (D) stereolithography, respectively[60].
Fused deposition modeling printing
Fused deposition modeling (FDM) is another classical example of extrusion-driven printing processing through which layer-by-layer deposition of thermoplastic filaments can be attained. Thermoplastic filaments are heated to semi-molten conditions before they are extruded via nozzle on the substrate to develop 3D architectures[61,62]. The different processing parameters utilized in the FDM printing process are layer height, wall thickness, infill pattern, infill density, printing speed, extrusion temperature, raster angle, raster width, and build orientation. FDM is the most frequent 3D printing process and is widely deployed in stationaries, toys, creative gifts, and training aids owing to its low costs and simple operation characteristics. In comparison to DIW printing process, FDM has a narrow window of printable materials and generally needs thermoplastic filaments such as polyamide, acrylonitrile butadiene styrene, thermoplastic urethane, polycarbonate, and polylactic acid. These reported thermoplastic materials cannot be considered to develop sustainable electrodes for MSCs and MBs owing to their inferior electrical conductivity characteristics. Thus, to manufacture high-performance and sustainable MEESDs, it is required to consider and design useful filaments for FDM process. Various approaches have been reported to alter the basic characteristics of thermoplastic filaments in order to make them useful candidates for MEESDs; e.g., thermoplastic polymer matrices can be manipulated by mixing them with highly electroactive conductive materials. Besides this approach, electrochemical outcome of the extruded thermoplastic materials can also be enhanced by depositing advanced functional materials such as MXene and polypyrrole (PPy) or electrically conductive metals such as silver (Ag) and gold (Au)[60]. Furthermore, in comparison to DIW printing techniques, the FDM also has low printing resolution (in the range of 50-200 μm), inferior flexibility of multi-material capability, and a lower printing throughput [Figure 2B][60].
Inkjet printing
Inkjet printing (IJP) is a typical class of deposition process where materials are directly propelled in the form of droplets via a nozzle onto plastic or paper-based substrates[63]. This process is very much in similar to DIW printing, where printable ink is prepared first, which can be patronized by moving the printhead with nozzles across the provided platform with the assistance of the printer. The resolution of printed patterns is primarily ascertained by the rheological behavior of the utilized inks, along with the mechanism and physical operations related to the adopted fabricating process. In addition, the resolution of IJP printed patterns somehow also depends on the provided diameter of the printing nozzle, but a smaller diameter is costly to afford and more likely can cause clogging of the nozzle during printing process. Based on generated droplets, IJP currently has two main contemporary classes, namely continuous inkjet (CIJ) and drop-on-demand (DOD) IJP. By considering the working principle of CIJ, a continuous stream of printing droplets is generated under certain applied pressure and spread out on the provided platform. In comparison to DOD, the diameter of the droplet in CIJ is marginally bigger than that of printing nozzle, resulting in an inferior resolution of the printed architectures. In contrast to CIJ, DOD has many advantages, e.g., HR, low operating costs, and atmosphere friendliness. In detail, the main reason of attaining HR of 20 μm is owing to pressure pulses created by piezoelectric or thermal printing heads. IJP inks also have some specific requirements in terms of dynamic viscosity and surface tension for printing process with reported much lower viscosities (typically in the range of 40 to 100 cP) than those deployed in DIW printing process. For productive control during the operation of printing process, a proper understanding of the ink behaviors outlining droplet formation, their spread processes, synergistic interactivity between the depositing droplet and the utilized substrate, and defect-free solidification process of droplets after deposition can impart significant roles[64,65]. In comparison to FDM, abundant electroactive materials can be deposited through IJP printing process to develop MEESDs; however, the as-fabricated MEESDs are usually fabricated as thin films owing to low viscosities of utilized inks and size capability, which restricts the design and development of sustainable 3D-structured electrode materials [Figure 2C].
Stereolithography printing
Stereolithography (SLA) printing is a typical printing technique, which is purely based on photopolymerization process that produces the predefined 3D architectures by the application of a pre-designed scanning route of ultraviolet (UV) or visible laser source to the photoresin (typically acrylic or epoxy-based resin) followed by a solidification process[66,67]. Usually, photosensitive precursor materials are based on two prominent components: a photoinitiator and a prepolymer material. In detail, UV light inaugurates the photopolymerization process of the respective resin, which then resulted in the formation of 2D single-layer cross-section after following the solidification process. The building platform unit moves vertically (upwards or downwards) to develop a monolithic component covered by a fresh layer of the liquid resin following the source of photo medium (UV or visible light), wherein the moving distance of the build platform is predefined by the height of the layer. The prominent processing parameters that can affect the quality of SLA-printed objects are fill cure-depth, layer thickness, and post-curing. Through SLA printing process, 3D objects are completed with the assistance of each newly cured layer according to the pre-designed model of the architecture. After the process, these objects are washed properly with appropriate solvent to remove the wet uncured resign from their respective surfaces before the post-processing is initiated. However, for the smooth completion of the process, photopolymerization process should involve a perfect photoinitiation process and support a fast-crosslinking process, so that on exposure to light, solidification of liquid resin should immediately occur to form highly cross-linked networks[68]. Therefore, the right ratio of photoinitiators and prepolymer materials in the liquid resin is very crucial. Considering the working mechanism of SLA printing process, the printable resins are aggregates of photoinitiators, prepolymers materials, and electroactive materials. Moreover, in comparison to other printing techniques such as DIW, IJP, and FDM, the SLA technique has lower resolution and can print objects with a minimum feature size of approximately 0.5 mm. The prominent areas of application of SLA in the development of MEESDs include: (i) the preparation of collectors and substrates to fill electrode materials or deposit conductive layers; and (ii) blending of light-treatable polymeric materials with electroactive materials. In contrast to IJP and DIW printing processes, SLA does not rely on nozzles to develop printed objects; thus, it does not have any conventional clogging problems [Figure 2D]. SLA printing process has various advantages such as being easy to operate and having improved resolution; however, its commercial application is highly restricted and minimal owing to the handling of sticky and messy processes involved in preparing photopolymers.
2D MATERIALS FOR SUSTAINABLE 3D-PRINTED MICROSTRUCTURES
Distinct characteristics
Owing to unique printing aspects of DIW process, the importance of 2D materials will be disclosed in relation to the preparation of sustainable and high-performance 3D-printed architectures. For DIW, various steps starting with ink preparation, ink extrusion, deposition/solidification of extruded filament, post-processing cycles play a crucial role in the successful printing process of materials or devices. In contrast to other 3D printing processes, solidification of DIW-printed filament purely depends on self-supporting behaviors of printing inks. So, appropriate properties of printing inks become the most considerable requirement for continuous extrusion and sustainability of self-supported 3D-printed filaments[69]. In the meantime, to attain commendable electrochemical performance and high quality of DIW-printed MSCs and MBs, some important technical/scientific phenomena need to be addressed as disclosed followingly. Initially, ink composition should be rationally designed and formulated. In this regard, electroactive materials, additives (e.g., cross-linkers, binders, and fillers) and solvent mediums are the prominent components that are either physically or chemically mixed together to formulate the printing inks. Among various dimensional [zero-dimensional (0D), one-dimensional (1D), 2D, and 3D] available electroactive materials, 2D materials-based inks possess unique physicochemical characteristics. Their high electrical conductivity can accelerate electron transportation; enhanced specific surface areas can facilitate the adsorption of ions resulting in maximum capacitance, and tunable interlayer spacing supports ion intercalation. In addition to these pre-described physicochemical properties, these also have a large surface-to-volume ratio, recognized anisotropic properties, high mechanical strength and chemical stability, enhanced face-to-face stacking phenomena (with a large surface interaction that improves the intersheet interaction furthermore), shorter ion transportation pathways (supported by their exposed contact between microscale electrodes and electrolytes), and high aspect ratio (MXene ~4,000)[70-72]. All these pre-mentioned characteristics are quite important for the development of sustainable MEESDs.
Unique rheological properties and printing design freedom
In addition to the distinct merits of 2D-structured materials, appropriate ink rheological characteristics are fundamental requirements for the continuous ink fluidity and retainment of filament printed shape since inks have to undergo three prominent steps during DIW printing process, including flow of inks inside the syringe and nozzle, extrusion of the provided inks through the nozzle and subsequently deposition on the provided substrate. During the DIW printing process, a smooth flow of ink inside the syringe and nozzle must be ensured to avoid any kind of clogging during ink extrusion process. In general, the viscosities of printing inks decreased with increasing shear rates, which favors both processes namely ink flow from nozzle and ink extrusion. Furthermore, 2D materials-driven inks are proven to display shear-thinning characteristics by rationally designing the formulation of their respective solutions. In addition, it has also been reported that 2D materials contribute unique rheological properties mainly supported by their high aspect ratio. For instance, GO displayed an excellent modulus of elasticity of 350-490 Pa in water with a reported concentration of 13.3 mg mL-1 in comparison to the lower elastic modulus (~60 Pa) of 1D material-(single-walled carbon nanotube) SWCNT suspension with the same concentration[73]. Owing to several advantages associated with 2D-driven inks such as their unique rheological characteristics and ease of manipulating colloidal response, it is well concluded that 2D materials are the most appropriate contenders for manufacturing 3D architectures with required design and optimized electrochemical properties[74].
To date, development of 2D materials-driven microstructures via 3D printing process is mainly based on graphene-based microelectrodes, and GO-driven ink is commonly utilized. Generally, the viscoelastic characteristics of GO in water are mainly dependent on its concentration and have been extensively investigated to obtain different ink printabilities contributions according to the adapted process and purpose [Figure 3A-D]. In this context, Tian have concluded that with low concentrations
Figure 3. (A-D) storage moduli (G/) and loss moduli (G//) of graphene oxide (GO) suspensions of frequency at different concentration degrees; e.g., 0.05, 0.25, 0.75, and 13.3 mg mL-1, respectively[75]; (E) MXene-based inks (with various concentrations) shear thinning behaviors suitable for uninterrupted extrusion through printing nozzles (diameter ~250 µm); (F) inks viscosity evolution over time for alternate minimum (0.01 s-1) and maximum (1,000 s-1) shear rates, illustrating suitable viscosity drop and post-printing recovery; (G) inks’ viscoelastic fingerprints demonstrating their solid-like behavior with large plateau regions (where G′ is unhampered of stress) and yield stresses (overlap point between G′ and G″) that elevate as the inks become more thickened (concentrated)[79]; and (H) illustration of 2D materials-based 3D-printed architectures: serpentine electrode, woodpile electrode (scale-bar = 10 millimeter), rectangular-like hollow prism printed through 250 μm nozzle (number of printed layers = 25, reported scale-bar = 3 millimeter), and pectinate structure (two printed layers, scale-bar = 10 millimeter)/pyramid-like 3D-printed structure (number of printed layers = 12, scale-bar = 10 millimeter)/MXene printed font (three printed layers, scale-bar = 10 millimeter)[79,83,84].
Hybridization and post-processing treatments
The hybridization of advanced materials can facilitate synergistic effects to accelerate performance far beyond those consisting of individual components for the development of sustainable electrochemical energy storage. In this regard, 2D materials, such as graphene, own great potential as a building block for the development of 3D macroscopic architectures by the inclusion of various dimensional secondary materials (for instance, 0D, 1D, and 2D functional additives). However, to fully investigate the potential of these hybridized 3D structures, various parameters should be prioritized in the design process:
Figure 4. (A) Schematic illustration of 2D materials-based 3D-printed hierarchical structures; (B-i) FE-SEM images of (2D + 1D) graphene-CNTs mixed hybrid material at various magnifications (scale bar: 50 μm and 200 nm, respectively); (B-ii) TEM microstructure of graphene-CNTs mixed hybrid material with inset of schematic illustration of 2D + 1D hybrid material (scale bar:
The significance of post-processing steps in order to enhance the electrochemical contribution of DIW-printed architectures cannot be ignored. For 3D extruded microstructures, widely reported post-treatment processes such as thermal annealing, surface-functionalization, and surface polishing (or deposition) are deployed. As mentioned earlier, most of the graphene-driven DIW-printed microelectrodes are based on GO dispersions, hinting at the low electrical conductivity and inferior rate-capability of directly extruded GO filaments. In this context, Yao et al. deployed a unique combination of thermal annealing and surface functionalization in order to enhance the overall electrochemical contributions of 3D graphene aerogels (SF-3D GA)[86]. In detail, 3D-printed microstructures were properly freeze-dried and annealed at a temperature of 1,050 °C to transform GO aerogels into graphene-driven aerogels. In the next development step of SF-3D GA, the graphene aerogels were electrochemically oxidized in the presence of 0.5 M KNO3 solution in order to introduce surface functional groups for particular time of 3 h. Finally, surface functionalized 3D GA was further reduced in hydrazine hydrate (HH) solution (0.1%) for 1 h at 50 °C. The impact of electrochemical oxidation has not significantly changed the structure and nanosheets’ morphology of the 3D-printed architecture. However, HR-TEM microstructure clearly illustrates that crystallinity level of GSs reduces after the electrochemical oxidation process [Figure 4D and E]. Comparing SAED patterns (bottom inset of Figure 4D and E) also confirms the amorphous nature of the graphene nanosheets of the SF-3D GA sample. Moreover, contact angle measurements (top inset of Figure 4D and E) illustrate that 3D GA has changed from hydrophobic nature (~contact angle 140°) to hydrophilic (~contact angle 0°) after the commencement of electrochemical oxidation process. As per nitrogen adsorption-desorption isotherms, the SSA value of 3D GA architecture has also improved moderately from 78.3 to
2D MATERIALS FOR 3D-PRINTED MICRO-SUPERCAPACITORS
2D materials for 3D-printed EDLCs
Utilizing 2D materials as electrodes in EDLC-based MSCs offers a plethora of advantages that collectively contribute to the remarkable enhancement of device performance and capabilities[91]. Commonly, in EDLCs-driven MSCs, energy is physically stored via electrostatic charge adsorption at the two-phase interface existing between the electrolyte and electrode material. MSCs based on EDLC materials exhibit a lofty SSA value of 2,630 m2 g-1, excellent PD, phenomenal electronic conductivity, and unmatched cycle life[92]. Furthermore, these MSCs offer rapid charging and discharging rates, enabling efficient energy transfer within remarkably short timeframes[93]. The low internal resistance of EDLCs allows them to promptly respond to sudden energy requirements, positioning them as invaluable assets in applications requiring instantaneous surges of power, such as peak power compensation and the management of pulsed loads in electronic systems[94]. Considering the content of the article, herein, we have emphasized the importance of 2D-driven EDLC materials (e.g., graphene, graphene-driven composites, and GO) for the development of sustainable 3D-printed MSCs. In detail, various approaches have been disclosed in forthcoming sections deployed to fabricate high-performance and sustainable graphene-driven 3D-printed architectures. In this regard, Jiang et al. have fabricated graphene aerogel microlattices (GAMs), which show immense promise across multifunctional applications owing to their combination of low density, high porosity, precisely engineered lattice structures, exceptional elasticity, and adjustable electrical conductivity[95]. However, previous 3D printing methods for creating GAMs have been hindered by either the need for a high concentration of additives or intricate fabrication processes, limiting their widespread utility. This study introduces a straightforward ion-induced gelation technique for directly 3D printing GAMs using GO-based ink. By introducing a small quantity of Ca2+ ions as gelators, the aqueous GO solution undergoes a transformation into a printable gel ink. This ink is utilized to directly print self-supporting 3D structures, featuring programmable microlattices, within ambient air conditions at room temperature. The as-developed microlattices were freeze-dried to develop solid GO aerogel, which was further reduced in the exitance of hydrogen iodide (HI) to obtain cleaned 3D-printed graphene-driven microlattices [Figure 5A]. In order to study the mechanical behavior, compression tests were performed to gauge the compressive stress as a result of reported strain of the 3D-printed GO aerogel samples. Compression results show that the 3D-printed GO aerogels display phenomenal resilience when liberated from compression cycle. At 80% strain, 3D-printed GO architecture has displayed a compressive stress value of ~90 kPa [Figure 5B]. The resultant GAMs possess a complex hierarchical pore structure alongside high electrical conductivity, translating into impressive capacitive performance well-suited for supercapacitors. The cyclic voltammetry (CV) curves of the 3D graphene-driven supercapacitor (3DGC) electrodes produced using the formulated ink display near-square shapes, a clear indication of the expected performance associated with EDLC [Figure 5C]. The gravimetric capacitance of 3DGCs is reported to be 212 F g-1 at
Figure 5. (A) Schematic presentation of 3D printing process guided through the provided arrows; initially, a certain quantity of CaCl2 is inserted into GO solution to formulate GO ink inheriting appropriate rheological characteristics. In the next step, GO ink is squeezed out through a robot-controlled nozzle to develop 3D structure. Finally, the as-developed microlattices were properly freeze-dried to achieve solid graphene oxide (GO) aerogel, which is further reduced by HI to receive neat microlattices of graphene-printed aerogel; (B) the stress-strain curve for GO-driven microlattice; (C) CV curves of 3DGC-1 at varied scan-rate values; (D) rate-performance comparison for 3DGCs with various thickness[95]; (E) schematic presentation of 3D-printed graphene aerogel (denoted as GA) and graphene-mixed-dimensional hybrid aerogel (denoted as G-MDHA); in reported path 1, urea and GδL were mixed in the dilute GO suspension in order, accompanied by elevation of temperature to stimulate the gelation process assisted through controlled hydrolysis of urea during the evaporation of solvent (i and ii); subsequently the GO-driven ink was printed according to the designed architecture (iii); in the final step of path 1, the as-printed architecture was freeze-dried and chemically reduced to obtain graphene aerogel (iv and v). In route 2 of the same scheme, suspension based on multidimensional (e.g., 0D, 1D, and 2D) functional additives were added to the GO suspension, respectively, pursued by the identical treatment steps (i-v) adopted in step 1; finally extra annealing process (vi) was performed to develop G-MDHA[85]; and (F) cycling stability of G-CNT printed composite electrode material at 0.10 mA cm-2[91].
Another study conducted by Tang et al. has reported 3D-printed graphene aerogel and graphene-driven mixed-dimensional hybrid aerogels for supercapacitors[85]. Herein, the main disclosed concept is to illustrate the importance of graphene-driven mixed-dimensional (2D + 0D, 2D + 1D, and 2D + 2D) electrode materials for the evolution of high-performance 3D-printed electrode materials. The adopted procedures to control the rheological characteristic of the printing inks (GA and G-MDHA) and development of 3D-printed GA and G-MDHA architectures are well illustrated in Figure 5E. Further synthesis protocols of 3D GA and
2D materials for 3D-printed pseudocapacitors
Pseudocapacitors, a distinct subset within the realm of EESDs, have attracted substantial recognition due to their multifaceted advantages. These advantages originate from their unique electrochemical properties and structural characteristics, setting them apart from conventional capacitors and batteries[96,97]. Unlike typical EDLCs, the energy in pseudocapacitors is stored through faradic reactions, in which ultrafast and reversible oxidation/reduction reactions take place near or at the electrode/electrolyte interface[98-100]. Common 2D pseudocapacitive materials include conductive polymers, noble metals, metal oxides, and LDHs. As compared to EDLCs, 2D-driven pseudocapacitors have high potential to offer much more in terms of electrochemical contributions; however, their intrinsic electrochemical properties are mainly compromised due to their inferior electrical conductivity[101-103]. Nevertheless, with the progress in advancing research, there has been rapid growth in emerging 2D pseudocapacitive materials, e.g., MXenes (metal carbides/nitrides), MOFs, transition metal oxides (TMOs)/hydroxides (HOs), LDHs, dichalcogenides, and black phosphorus (BP) with much improved electrochemical contributions[104]. Considering the importance of advanced 2D materials, herein, we have disclosed and discussed the reported 3D-printed pseudocapacitors along with their key rheological, structural, and electrochemical characteristics. Huang et al. utilized MXene hydrogel for multi-scale structure engineering to fabricate supercapacitors[105]. As depicted in [Figure 6A], they employed a method involving H2SO4 to facilitate the unidirectional growth of MXene and synthesize H2SO4-thawed MXene hydrogel. During the thawing process of freeze-dried MXene, it was revealed that the contact angle of water decreased due to the influence of H2SO4, leading to faster electrolyte penetration and improved rate performance. The MXene hydrogel film thus produced was used to create printed electrodes using the DIW method. When comparing the electrochemical properties of the produced MXene, disordered MXene, H2SO4-based aerogel, and filter-based film, it was found that the ordered MXene illustrated the highest overall capacitance of 393.0 F g-1. Furthermore, it maintained a capacitance retention rate of 50% even when the scan rate elevated from minimum (100 mV s-1) to maximum (1,000 mV s-1) value, surpassing other electrodes by a significant margin [Figure 6B]. Additionally, it was determined that the Rct (charge transfer resistance) value was exceptionally low. This group engineered MXene hydrogel through multi-scale structural control to create unidirectionally grown MXene hydrogel for the application of supercapacitors[106]. They utilized 3D printing techniques to fabricate a honeycomb-like compartmentalized structure. This approach synergistically enhances the diffusion and mobility of electrolyte ions while increasing the available surface area for ion utilization. Zhou et al. used DIW technology to construct 3D architectures for EESDs, leveraging 2D MXene materials[84]. Conventional techniques often struggle to achieve such complex structures. However, there is a challenge in meeting specific rheological characteristics for 3D printing process, as it necessitates a notable quantity of MXene in the ink. This, in turn, leads to a self-restacking structure issue after drying. To address this challenge, the research introduces a range of cellulose nanofibers (CNFs) with varying surface chemistries and morphologies. These CNFs are employed to enhance the rheological properties of the MXene-driven inks, ensuring phenomenal 3D printability of the mixture. The attained optimized hybrid ink, with a low solid content, successfully facilitates the printing of various 3D structures, maintaining superior shape preciseness and geometric accuracy. Upon freeze-drying, these 3D structures become self-standing and hierarchically porous. Shrinkage of MXene occurs during this process, and to minimize it, a method involving adding CNTs was employed. As seen in [Figure 6C], this approach effectively reduced the thickness from the initial 0.44 mm to 0.43 mm after freeze-drying. It was reported that this transformation can enhance ion transport efficiency, surface area accessibility, and pseudocapacitive performance. When comparing the capacitive and diffusive distribution using this approach, it was confirmed to have a capacitance distribution of 69.82% [Figure 6D]. Upon checking the galvanostatic charge-discharge (GCD) profiles, a high Coulombic efficiency (CE) was observed, and nonlinear data characteristic of a pseudocapacitor was evident [Figure 6E]. In particular, a solid-state interdigitated symmetrical supercapacitor (SSC) is 3D-printed, achieving notable results. It exhibits an areal capacitance value of 2.02 F cm-2 with an ED of 101 μW h cm-2. Even after 5,000 cycles, the device delivers a capacitance retention rate of 85%. The research conducted by Yu et al. has induced a practical approach to fabricating multifunctional systems with precisely designed architectures[107]. In this context, 2D MXenes have gained considerable interest in the arena of printed energy storage devices. However, a significant challenge arises due to the van der Waals interaction between intrinsic MXene layers, leading to restacking problems within printed structures. These issues can substantially hinder ion and electrolyte transport, consequently affecting electrochemical performance. To address this challenge, the researchers demonstrate a melamine formaldehyde templating method to create crumpled nitrogen-doped MXene (N-MXene) nanosheets. The TEM observation in Figure 6F provides additional insights into the detailed structure of wrinkled N-MXene. Furthermore, HAADF-STEM images and the corresponding elemental mapping demonstrate the uniform distribution of native elements such as Ti, C, and N in the investigated area of doped-MXene. Nitrogen doping enhances electrochemical performance of MXene by improving redox activity and conductivity. Accordingly, two types of N-MXene inks are formulated, optimized for 2D screen printing and 3D extrusion printing processes. Doped-MXene displayed a pair of signature redox peaks relating to the protonation and change in the oxidation states of titanium atoms, indicating the typical pseudocapacitive behavior of MXene sheets. The screen-printed N-MXene MSC exhibits an areal capacitance value of 70.1 mF cm-2 while preserving excellent mechanical robustness. Moreover, the 3D-printed N-MXene-based supercapacitor, featuring a three-layered electrode, achieves an areal capacitance (Ca) of 8.2 F cm-2 and can store a high areal ED of 0.42 mW h cm-2. Furthermore, this research team achieved enhanced flexibility performance through the 3D printing of pseudocapacitors. They conducted experiments by varying the bending angles, as shown in Figure 6G. During these experiments, it was confirmed that the shape of the CV curve remained unchanged, indicating excellent mechanical robustness [Figure 6H]. Moreover, these flexible cells also demonstrate a high cycle stability with a capacitance retention rate of 92% even after 7,000 cycles, showcasing their remarkable long-term durability. Orangi et al. made self-powered and miniaturized energy storage devices that can contribute commendable power and energy densities within limited space availability[108]. In this study, the researchers present a novel approach for the development of all-solid-state MSCs (SS-MSCs) using a 3D printing technique with the support of additive-free and water-driven MXene ink. The as-developed MSCs benefit significantly from the exceptional electrochemical properties and high electrical conductivity of Ti3C2Tx materials. These materials, combined with a 3D interdigital electrode architecture, enable the MSCs to achieve remarkable volumetric and areal energy densities. The key innovation in this research study is the application of a highly-concentrated MXene ink with preferable viscoelastic characteristics, enabling extrusion printing process at room temperature. This approach facilitates scalable manufacturing of MSCs with various architecture designs and electrode thicknesses, even on a range of substrates, including flexible ones such as polymers and paper. The electrochemical outcome of the printed solid-state devices (PSSDs) was outstanding, with high Ca of up to approximately 1,035 mF cm-2, showcasing their potential for sustainable energy storage applications. The innovative approach to harnessing versatile N-MXene inks provides profound intuition into the development of printed electrical equipment safety schemes (EESSs) characterized by high areal ED and scalability, paving the direction for the advancement of next-generation sustainable energy storage systems. Moreover, the key electrochemical performance of reported 2D materials for 3D-printed pseudocapacitors has been well summarized in Supplementary Table 1.
Figure 6. (A) Schematic illustration of MXene hydrogel supercapacitor electrode; (B) rate performance of the MXene hydrogel, unordered hydrogel, H2SO4-immersed aerogel, and filtrated MXene film[105]; (C) Top view SEM micro-structure of 3D-printed MXene; (D) CV graphs at 50 mV s-1 while the blue-colored area illustrating the surface capacitive contributions; (E) GCD graphs at different current density (CD) values[84]; (F) TEM image of crumpled MXene-N nanosheets and HAADF-STEM elemental maps of N-doped MXene sheets; (G) digital photographs; and (H) CV graphs of N-doped MXene printed MSC under different bending angles[107].
2D materials for 3D-printed hybrid capacitors
Considering the individual electrochemical characteristics of EDLC- (high PD) and pseudocapacitor-driven (potential to deliver high ED) MSCs, their intrinsic lower energy contributions (~capacity to store energy per unit weight) are not up to the mark to consider them as alternatives to batteries at commercial scale[109]. However, the combination of EDLCs and pseudocapacitive-driven materials, such as graphene, MXenes, TMDs, TMOs, LDHs, and MOFs in the hybrid form can deliver high ED without compromising the intrinsic high PD characteristics of supercapacitors. Hybrid capacitors employing 2D materials as active components are currently under active investigation. Utilizing 2D hybrid materials through advanced manufacturing process such as DIW 3D printing process, sustainable 3D architectures can be constructed [Figure 7A], possessing special characteristics such as high porosity, low density, and adjustable electrical conductivity. The integration of hybrid materials with the DIW method demonstrates superior capacitive performance compared to conventional bulk electrodes. Herein, their potential for application in microdevices through patterning has been revealed and discussed in detail. In the study by Zhao et al., a highly electroactive Cu/Co-THQ@CNTs@GO (THQ: tetrahydroxy-1,4-quinone) microlattice electrode was applied to LIC (Lithium-ion Capacitor)[110]. The electrodes were manufactured using 3D printing, with a diameter of approximately
Figure 7. (A) Schematic illustration of making the 3D structure microlattices and hybrid capacitors; (B) SEM image of 3D structure electrode and SEM-EDX; (C) typical charging/discharging graphs of printed microlattices with various printed layers[110]; (D) capacitance plots with different mass loadings[111]; (D-i-D-iii) microstructural analyses with the increase of NiCo2O4 content; (E) CV curve of hybrid-capacitor electrode material; and (F) corresponding areal and volumetric capacitances at different current densities.
2D MATERIALS FOR 3D DIW-PRINTED MICRO-BATTERIES
2D materials for 3D-printed Li-based batteries
Li-based batteries have presented themselves as potential candidates to empower electric vehicles or portable gadgets owing to their high ED and lengthy cyclic life contributions[115-117]. However, commercially available Li-based batteries also display confined electrochemical outcomes mainly due to the application of conventional electroactive materials and their basic reported geometries such as pouch cells, prismatic, coin, and cylinder. To develop high-rated Li-driven batteries, application of advanced electroactive materials, proper design, and manufacturing process of various battery modules such as anodes/ cathodes, separators, and electrolytes can play significant roles[60]. In this regard, development of Li-based batteries based on 2D electroactive materials through advanced manufacturing processes such as DIW printing process is heavily under investigation[118]. This unique combination has resulted in the formation of well-patterned microstructures for Li-driven batteries with sustainable electrochemical contributions to meet the advanced energy storage milestones. The key factors which help to attain such prominent electrochemical performance are outlined as follows; (i) 3D printing process enables the deposition of high areal mass loadings of electroactive materials; (ii) availability of shorter ion-diffusion pathways in the printed architecture; (iii) formation of sufficiently deep porous architectures, facilitating the storage of electrolyte solution during redox process proceedings; (iv) providing opportunity to fabricated complex printed architectures with required design and dimensions; and (v) 2D materials physical/chemical characteristics help to develop mechanically sustainable 3D architectures[119-121]. Regarding the formation of 3D-printed architectures based on 2D materials, various studies, along with their key results and findings, have been disclosed and summarized as follows. Sun et al. have mixed rGO, silver nanowires (AgNWs) and lithium tin oxide (LTO) to fabricate thick-electrode material demonstrating phenomenal areal capacity value and rate performance for 3D-printed lithium-ion batteries[122]. They control the areal capacity contributions of the reported electrode material with the number of its deposited ink layers (thickness ranging from 150 to 1,500 μm). Benefitting from a highly conductive AgNW network embedded in the 3D-printed graphene scaffold structure, they reported a high areal capacity value of up to 4.74 mAh cm-2 with a maximum electrode thickness of 1,500 μm (~10 deposited layers) [Figure 8A]. In comparison, rGO-LTO binary 3D-printed composite electrode material can display only half of the areal capacity value with a maximum electrode thickness of 900 μm. Graphical presentation of electron and ion transportation kinetics occurring in the 3D-printed architecture of rGO-AgNWs-LTO-driven electrode is displayed in Figure 8A(A-i) and is described through the following enlisted points. Firstly, the open mesh architecture
Figure 8. (A) Gel-based thick electrode fabrication mixing with 2D materials realization of high mass loading electrode[122]; (A-i) graphical presentation of the electrons and ions movement behavior in 3D-printed rGO-AgNWs-LTO electrodes and discharging process of respective material for lithium metal battery system; (B) schematic diagram of lithium sulfur copolymer for 3D printing[124]; (B-i) SEM microstructure of 3DP-pSG architecture from top; (B-ii) lateral view of the architecture disclosing layer-by-layer deposition of stacked filaments; (C) schematic diagram of 3D printing architecture for high loading lithium sulfur battery[125]; (C-i) cycling contributions of Li-S coin cell assembled through 3D-PC with maximum sulfur areal loadings of 10.2 mg cm-2 at 0.2 C; (C-ii) assembly illustration of bracelet-like battery; (D) schematic presentation of 3D printing process of LFP and MXene ink for lithium metal batteries[127]; (D-i) schematic presentation of freeze-drying process for the development of porous MXene microlattices; (D-ii) top-view of the as-developed porous MXene lattices; (D-iii) cycling life contributions of MXene@Li and Cu@Li anodes-driven symmetric cells (SCs) with a plating/stripping capacity of 1 mAh cm-2 at 1 mA cm-2; (D-iv) cycling life comparison of MXene@Li electrode with earlier documented 3D-printed architectures deployed for lithium metal anodes (LMA) at 1 mA cm-2; (D-v) rate-capability contributions of MXene@Li-based symmetric-cell (evaluated from 1 to 30 mA cm-2 for 60 min); (d-vi) cycle time of symmetric cell MXene@Li cells at 30 mA cm-2 and areal capacity of 30 mAh cm-2; and (D-vii) the areal capacity of 80 mAh cm-2 at
In order to fulfill the high ED demands for the development of modern wearable microelectronic and electric vehicle systems, conventional lithium-ion batteries are being replaced by other efficient systems such as Li-sulfur (S), Li-air, and lithium metal batteries (LMBs). Herein, considering the importance of these advanced systems, we have discussed the prominent studies covering the core subject of this review article. In comparison to conventional lithium-ion batteries, LMBs based on sulfur cathode materials possess excellent theoretical ED up to 2,600 Wh kg-1[123]. Moreover, sulfur also exists abundantly in nature and is atmosphere-friendly. In this regard, 3D sulfur copolymer-graphene architectures (3DP-pSG) with well-arranged microlattices have been reported by Shen et al. for Li-S batteries. Process involved in the development of 3D-printed sulfur copolymer-graphene (3DP-pSG) architectures is well-illustrated in Figure 8B[124]. After the preparation of GO/S/DIB-driven ink, it was poured into a 3 mL syringe to initiate a printing process of layered-by-layered architectures. In the final prominent synthesis step, the sulfur copolymer was grown on the graphene nanosheets by exposing the 3D-printed architecture to 200 °C for a specific reaction of time. The SEM microstructures of (3DP-pSG) architecture covering its top and lateral views are displayed in Figure 8B(B-i). Top-view of the 3DP-pSG architecture clearly illustrates the existence of well-defined macropores, which were developed from continuous filaments with an average diameter of 200 μm. Moreover, top-view analysis also confirms the structural coherence of the 3D-printed architecture despite the fact that it was exposed to a thermal treatment. The lateral view of the architecture demonstrates the existence of well-diffused six printed layers with a constant thickness of 100 μm for each layer, facilitating sustainable mechanical stability to the whole architecture. In comparison to 3DP-SG (specific capacity value ~680.7 mA h g-1), the 3DP-pSG architecture has contributed a phenomenal specific capacity value of 812.8 mA h g-1. Moreover, with the increase of CD from minimum to maximum values
Other prominent systems that have the capacity to replace traditional lithium-ion anode materials (e.g., graphite, which owns a maximum theoretical specific capacity value of ~372 mA h g-1) are lithium metal-driven anode materials with an ultrahigh theoretical specific capacity value of ~3,860 mA h g-1 and very low redox potential [-3.040 V vs. SHE (standard hydrogen electrode)][126]. However, several hurdles should be properly addressed prior to the utilization of lithium metal-driven anode materials for rechargeable LMBs, e.g., (i) uncontrollable growth of Li dendrites, which can raise various safety issues; (ii) generation of thick solid electrolyte interphase (SEI) on the lithium metal surface, resulting in maximum internal charge resistance; and (iii) large morphological and volumetric changes can take place in lithium metal anodes during repeated number of plating and stripping cycles. In order to control the aforementioned issues,
2D materials for 3D-printed next-generation batteries
Extensive research is under progress on next-generation batteries (such as zinc-ion batteries, sodium-ion batteries, and vanadium redox flow (VRF) batteries) to present them as an alternative to the Li-based batteries[132]. There are various advantages associated with such batteries. For instance, sodium-ion batteries have the potential to replace lithium batteries owing to high abundance of sodium (~the 4th most excessive element in the earth's crust)[133,134]; likewise, zinc-ion batteries and VRF batteries have also presented themselves as potential contenders in electrochemical energy storage systems owing to their low price, inherent protection, rich reserves, and echo-friendly-mode, safe in operations and ultra-long cycling life contributions, respectively[135-137]. The exploration of the advantages offered by 2D materials in next-generation 3D-printed batteries illuminates their transformative potential in energy storage applications. With enhanced electrical conductivity, superior electrochemical performance, mechanical flexibility, and materials diversification capabilities[138], the findings from this study underscore the significance of ongoing research and development efforts aimed at fully harnessing the potential of 2D materials, driving the progress of sustainable and high-performance energy storage solutions for the future[139]. Wang et al. made significant strides by harnessing state-of-the-art 3D printing technology to create V2CTx/rGO-CNT MXene microgrid aerogels, which serve as a highly promising matrix for sodium metal anodes [Figure 9A][140]. The intricate 3D-printed microgrid structures offer a hierarchical porous framework that not only ensures the utmost stability of the whole electrode during repetitive plating and stripping processes but also facilitates a vast surface area. This expanded surface area aids in reducing the CD and offers numerous active sites, fostering efficient sodium metal nucleation. In-situ transmission electron microscopy (TEM) characterization on V2CTx/rGO-CNT electrodes to delve deeper into the intriguing phenomenon of sodium metal deposition. This analytical approach was compared with the selected area electron diffraction (SAED) pattern after sodium deposition [Figure 9B]. It reveals the diffraction patterns of Na2O and NaOH. The emergence of these new patterns strongly suggests an intricate interaction between sodium and the V2CTx surface functional groups (=O and -OH), leading to the formation of inorganic compounds, Na2O and NaOH. This intriguing finding provides valuable insights into the complex chemical transformations occurring at the V2CTx surface during the sodium deposition process. The current study highlights the advancements made with the 3D-printed V2CTx/rGO-CNT electrode, which is comprehensively compared to different MXene-driven sodium metal electrodes and 3D-printed sodium metal electrode architectures in terms of electrochemical performance [Figure 9C]. Remarkably, the 3D-printed V2CTx/rGO-CNT electrode exhibits exceptional long cycle life, particularly under high CDs and large areal capacities, extending up to 50 mA h cm-2. This remarkable finding emphasizes the recognition of the application of 2D materials in 3D printing for next-generation batteries. Li et al. have successfully synthesized a composite electrode comprising rGO and Super-P aerogel for VRF batteries [Figure 9D][141]. This electrode exhibits a controllable porous structure and was created using the DIW printing technique. The uniform distribution of Super-P on rGO sheets is believed to contribute significantly to the improvement of electrode performances. The voltage efficiency (VE) and CE variations for cells incorporating different materials
Figure 9. (A) SEM image of the 30% V2CTx/rGO-CNT microgrid aerogel; (B) SAED patterns of V2CTx/rGO-CNT after sodium deposition; (C) radar-charts illustrating electrochemical performance comparison of various MXene-based sodium metal anodes[140]; (D) SEM surface morphology of rGO-P; (E) VE and CE of cells (with rGO, rGO-P (4:1), rGO-P (3:1) and rGO-P) at 80 mA cm-2; (F) energy efficiency (EE) curves at various current density values[141], XPS spectra of 3DP-FeVO/rHGO cathodes for (G) V 2p3/2 and (H) Fe 2p3/2; and (I) areal capacities of 3DP-FeVO/rHGO with varied number of printing-layers (at 6 mA cm−2)[142].
As explained earlier comprehensively about the importance of ZIBs, in this regard, Ma et al. have managed to attain improved performance of 3D printable ink, which was comprised of iron vanadate and reduced holey GO (rHGO). It is noteworthy that cellular cathode material with hierarchical porous structure for aqueous ZIBs was designed and manufactured by 3D printing process for the very first time[142]. To elucidate the electrochemical reactions occurring during the charging and discharging of 3DP-FeVO/rHGO cathodes, ex-situ X-ray Photoelectron Spectroscopy (XPS) of Vanadium (V) and Iron (Fe) at three distinct stages: the initial state, the discharged state (0.4 V), and the charged state (1.6 V) for the first cycle were performed
Figure 10. (A) Digital photo illustration of the 3D-printed rGO aerogel microelectrode placed on a flower; (B) XPS full spectrum of the 3DP-NGA with various N2 plasma treatment durations; (C) binding energies of Na atoms with pyridinic-N, pyrrolic-N, graphitic-N, and graphene by DFT calculations[143]; (D) ex-situ XRD spectrums of NVPF cathode material evaluated at various voltages; (E) GCD graphs reported at 1 C, (F) ex-situ XRD spectrums of NTP anode material attained at various voltages[144]; (G) simulation model of the current density (CD) dispersal on the surface of the 3D-printed rGO/CNT porous microlattice aerogel (p-MLA); (H) schematic presentation of Na nucleation/plating behavior on printed rGO/CNT microlattice aerogel; and (I) nucleation overpotentials of the electrodes at different CD values[145].
To meet the advanced requirements of the fast-growing miniaturization industry, researchers/scientists are always on the move to design and fabricate novel 3D-printed energy storage systems to attain the required results. In this regard, Ma et al. have achieved a significant milestone by successfully creating fully
CONCLUSIONS AND PERSPECTIVES
Sustainable 3D architectures with complex structures cannot be produced via ordinary dimensional materials and conventional manufacturing techniques. However, with the aid of 2D materials, advanced printing technologies possess recognizable potential to fabricate miniaturized EESDs to meet the requirements of the fast-growing electronics industry. Herein, after a brief introduction of 3D printing process, first, we summarized various 3D printing technologies along with their key advantages and disadvantages, followed by emphasizing extrusion-based DIW process and rheological characteristics of 2D materials-driven inks. From a rheological characteristics point of view, the printing inks with higher elastic modulus (G//G// > 1) can be appropriate for 3D DIW printing process. In this regard, binder-free modern materials, such as MXene, can help attain optimum viscoelastic behavior with moderate concentrations, mainly owing to their high aspect ratio (~4,000). Moreover, other key parameters disclosing the unique relationship between 2D materials and DIW printing process for the development of high-performance MEESDs have also been disclosed in detail. Additionally, 2D materials-driven 3D-printed architectures contribute unique characteristics which are summarized through the following discussed multiple points:
Considering the particular subject of the current study, promising developments have been reported with exciting results; however, this research topic remains in the early stages of evolution, and several prominent challenges exist and are suggested to be pondered in the future.
- Inactive binders or additives can restrict and deteriorate electrochemical performance of MEESDs, so immense efforts should be devoted to designing and applying advanced additive-free electroactive materials such as 2D MXenes. Such materials with excellent electrical conductivity, good rheological characteristics, and enriched redox contributions are highly recommended to develop sustainable miniaturized EESDs through DIW process.
- Although 3D DIW printing process offers an opportunity to develop high-performance microelectrodes from an electrochemical point of view, these can lack mechanical stability due to the generation of unavoidable porosity during the printing process. In addition, existence of an interface between the adjacent printed layers can cause large residual stresses in the printed microlattice architectures, which can also deteriorate their mechanical integrity rapidly. To avoid such circumstances, 2D-driven advanced composite inks in the existence of appropriate reinforcing additives or by applying post-treatment processes, such as additional thermal treatment, can be a suitable strategy to attain mechanically stable printed architectures.
- Importance of porous and well-interconnected hierarchical electrode materials cannot be denied as these facilitate shorter charge carrier pathways for the ultrafast movement of electrons/ions during electrochemical measurements and can effectively upgrade the electrochemical contribution of electrode materials. However, it is not an easy task to build highly porous hierarchical structures at the nano- or microscale. Therefore, more efforts are required to be devoted to manufacturing novel HR 3D-printed architectures with a lot of liberty to attain any required design and dimensions (nano/microscale). In this regard, combination of 2D-driven composite materials and 3D DIW printing process can be a vital breakthrough to generate hierarchically structured porous MEESDs with required ideal results.
- In recent times, 3D all-printed MEESDs have been manufactured by layer-by-layer deposition of the electroactive material, the current collector, and electrolyte inks via multi-nozzle DIW printing process. In realization of the development of safe 3D all-printed MEESD packages, a few challenges such as the leakage of moisture/air need to be resolved. Application of integrated, hybrid printing strategy can be vital in this regard.
- CE of the 3D-printed MEESDs is on the lower side in comparison to conventional bulk devices; owing to this drawback, the performance of the device can deteriorate at a faster rate, resulting in the failure of the microelectronics systems. In order to overcome this critical issue, it is required to mitigate the irreversible reactions by applying appropriate ink materials, controlling the porosity in the electrode architectures, modifying the surface chemistry of the electroactive materials, and regulating the electrolyte solutions.
- In the existence of 2D materials building blocks, advanced hierarchical microstructures need to be synthesized in order to empower the overall electrochemical output (such as ED, PD, and cycling stability) of printed hybrid supercapacitors. Moreover, void space is available in terms of the development of efficient next-generation flexible batteries with the aid of versatile manufacturing processes such as DIW printing techniques and highly versatile 2D-driven composite materials.
- Numbers of DIW-manufactured 2D-driven materials have been reported for MEESDs (e.g., MBs and MSCs); however, in-depth intrinsic electrochemical energy storage mechanisms (EES-Ms) have not yet been revealed comprehensively. It is widely established that the electrochemical contribution of printed electrode materials is highly related to their geometries. DIW printing process offers a good platform to digitally control the geometries of the electrode materials, wherein the energy storage mechanisms can be willingly investigated during the charge and discharge cycles. In this context, it is expected to devote more efforts to further boost the understanding of energy storage mechanisms.
- Integration of high-performance 3D-printed MEESDs with energy monitoring systems and energy harvesting systems is a potential research direction to consider in the future.
Thus, we emphasize that 3D printing process such as DIW with better resolution, application of a wide range of 2D materials, scalability, versatile production opportunities, and low cost will disclose new avenues in material designing and freedom to construct architectures for advanced MEESDs exhibiting excellent overall electrochemical performance, reliable mechanical strength, and customizable electrode configurations for other broad applications (such as miniaturized biomedical devices, microrobots, and flexible micro-electronics).
DECLARATIONS
Authors’ contributions
Conceptualization, methodology, writing-original draft, revision, review & editing: Saeed G
Writing-original draft, investigation, visualization, data curation: Kang T, Byun JS
Visualization, literature survey, data curation: Min D, Kim JS
Visualization, investigation, data curation: Sadavar SV
Supervision, investigation, writing-review & editing: Park HS
Availability of data and materials
The data is available upon request.
Financial support and sponsorship
This work was financially supported by the National Research Foundation of Korea (NRF) grant funded by the Korean government (MSIT) (No. NRF-2020R1A3B2079803).
Conflict of interests
All authors declared that there are no conflicts of interest.
Ethical approval and consent to participate
Not applicable.
Consent for publication
Not applicable.
Copyright
© The Author(s) 2024.
REFERENCES
1. Zhu M, Schmidt OG. Tiny robots and sensors need tiny batteries-here’s how to do it. Nature 2021;589:195-7.
2. Yu L, Li W, Wei C, Yang Q, Shao Y, Sun J. 3D printing of NiCoP/Ti3C2MXene architectures for energy storage devices with high areal and volumetric energy density. Nanomicro Lett 2020;12:143.
3. Jin J, Geng X, Chen Q, Ren TL. A better Zn-Ion storage device: recent progress for Zn-Ion hybrid supercapacitors. Nanomicro Lett 2022;14:64.
4. Hur JI, Smith LC, Dunn B. High areal energy density 3D lithium-ion microbatteries. Joule 2018;2:1187-201.
5. Zhang P, Wang F, Yu M, Zhuang X, Feng X. Two-dimensional materials for miniaturized energy storage devices: from individual devices to smart integrated systems. Chem Soc Rev 2018;47:7426-51.
6. Pan X, Hong X, Xu L, Li Y, Yan M, Mai L. On-chip micro/nano devices for energy conversion and storage. Nano Today 2019;28:100764.
7. Liu H, Zhang G, Zheng X, Chen F, Duan H. Emerging miniaturized energy storage devices for microsystem applications: from design to integration. Int J Extrem Manuf 2020;2:042001.
8. Jia R, Shen G, Qu F, Chen D. Flexible on-chip micro-supercapacitors: efficient power units for wearable electronics. Energy Stor Mater 2020;27:169-86.
9. Sumboja A, Liu J, Zheng WG, Zong Y, Zhang H, Liu Z. Electrochemical energy storage devices for wearable technology: a rationale for materials selection and cell design. Chem Soc Rev 2018;47:5919-45.
10. Chang Kim M, Saeed G, Alam A, et al. Ultrafine nanoparticles of tin-cobalt-sulfide decorated over 2D MXene sheets as a cathode material for high-performance asymmetric supercapacitor. J Ind Eng Chem 2023;124:294-303.
11. Zhang L, Yu L, Li OL, et al. FeF3·0.33H2O@C nanocomposites derived from pomegranate structure as high-performance cathodes for sodium- and lithium-ion batteries. Jops 2022;547:232014.
12. Yu L, Kim KS, Saeed G, Kang J, Kim KH. Hybrid ZnSe-SnSe2 nanoparticles embedded in N-doped carbon nanocube heterostructures with enhanced and ultra-stable lithium-storage performance. ChemElectroChem 2021;8:4732-44.
13. Brown E, Yan P, Tekik H, et al. 3D printing of hybrid MoS2-graphene aerogels as highly porous electrode materials for sodium ion battery anodes. Mater Design 2019;170:107689.
14. Delmas C. Sodium and sodium-ion batteries: 50 years of research. Adv Energy Mater 2018;8:1703137.
15. Zhu Z, Kan R, Hu S, et al. Recent advances in high-performance microbatteries: construction, application, and perspective. Small 2020;16:e2003251.
16. Zhang L, Liu D, Wu Z, Lei W. Micro-supercapacitors powered integrated system for flexible electronics. Energy Stor Mater 2020;32:402-17.
17. Chhowalla M, Shin HS, Eda G, Li LJ, Loh KP, Zhang H. The chemistry of two-dimensional layered transition metal dichalcogenide nanosheets. Nat Chem 2013;5:263-75.
18. Peng X, Peng L, Wu C, Xie Y. Two dimensional nanomaterials for flexible supercapacitors. Chem Soc Rev 2014;43:3303-23.
19. Shao M, Zhang R, Li Z, Wei M, Evans DG, Duan X. Layered double hydroxides toward electrochemical energy storage and conversion: design, synthesis and applications. Chem Commun 2015;51:15880-93.
21. Novoselov KS, Geim AK, Morozov SV, et al. Electric field effect in atomically thin carbon films. Science 2004;306:666-9.
22. Zhang Y, Tan YW, Stormer HL, Kim P. Experimental observation of the quantum Hall effect and Berry's phase in graphene. Nature 2005;438:201-4.
23. Akinwande D, Petrone N, Hone J. Two-dimensional flexible nanoelectronics. Nat Commun 2014;5:5678.
24. Ambrosi A, Pumera M. 3D-printing technologies for electrochemical applications. Chem Soc Rev 2016;45:2740-55.
25. Qiu L, He Z, Li D. Multifunctional cellular materials Based on 2D nanomaterials: prospects and challenges. Adv Mater 2018;30:1704850.
26. Garg R, Agarwal A, Agarwal M. A review on MXene for energy storage application: effect of interlayer distance. Mater Res Express 2020;7:022001.
27. Li K, Liang M, Wang H, et al. 3D MXene architectures for efficient energy storage and conversion. Adv Funct Mater 2020;30:2000842.
28. Talaie E, Bonnick P, Sun X, Pang Q, Liang X, Nazar LF. Methods and protocols for electrochemical energy storage materials research. Chem Mater 2017;29:90-105.
29. Zhou X, Cao A, Wan L, Guo Y. Spin-coated silicon nanoparticle/graphene electrode as a binder-free anode for high-performance lithium-ion batteries. Nano Res 2012;5:845-53.
30. Zheng S, Shi X, Das P, Wu ZS, Bao X. The road towards planar microbatteries and micro-supercapacitors: from 2D to 3D device geometries. Adv Mater 2019;31:e1900583.
31. Wang Z, Chen Y, Zhou Y, Ouyang J, Xu S, Wei L. Miniaturized lithium-ion batteries for on-chip energy storage. Nanoscale Adv 2022;4:4237-57.
32. Zhang W, Liu H, Zhang X, Li X, Zhang G, Cao P. 3D printed micro-electrochemical energy storage devices: from design to integration. Adv Funct Mater 2021;31:2104909.
33. Jabbar Khan A, Mateen A, Khan S, et al. 3D printed micro-electrochemical energy storage devices. Batteries Supercaps 2023;6:e202300190.
34. Bounor B, Asbani B, Douard C, Favier F, Brousse T, Lethien C. On chip MnO2-based 3D micro-supercapacitors with ultra-high areal energy density. Energy Stor Mater 2021;38:520-7.
35. Xu Y, Sheng K, Li C, Shi G. Self-assembled graphene hydrogel via a one-step hydrothermal process. ACS Nano 2010;4:4324-30.
36. Xiong C, Li B, Lin X, et al. The recent progress on three-dimensional porous graphene-based hybrid structure for supercapacitor. Compos Part B-Eng 2019;165:10-46.
37. Ashby DS, Deblock RH, Lai C, Choi CS, Dunn BS. Patternable, solution-processed ionogels for thin-film lithium-ion electrolytes. Joule 2017;1:344-58.
38. Alam A, Saeed G, Kim KH, Lim S. Metal-organic framework-derived NiS@Cobalt-Molybdenum layered double hydroxides shell@core as cathode and CoFe2O4-nanoparticles@MXene shell@core as anode materials for ultra-high energy-density flexible asymmetric supercapacitor. J Energy Stor 2022;55:105592.
39. Soram BS, Dai JY, Thangjam IS, Kim NH, Lee JH. One-step electrodeposited MoS2@Ni-mesh electrode for flexible and transparent asymmetric solid-state supercapacitors. J Mater Chem A 2020;8:24040-52.
40. Wang L, Wang Q, Jia W, Chen S, Gao P, Li J. Li metal coated with amorphous Li3PO4 via magnetron sputtering for stable and long-cycle life lithium metal batteries. J Power Sources 2017;342:175-82.
41. Gandla D, Tan DQ. Progress report on atomic layer deposition toward hybrid nanocomposite electrodes for next generation supercapacitors. Adv Mater Inter 2019;6:1900678.
42. Saeed G, Kumar S, Kim NH, Lee JH. Fabrication of 3D graphene-CNTs/α-MoO3 hybrid film as an advance electrode material for asymmetric supercapacitor with excellent energy density and cycling life. Chem Eng J 2018;352:268-76.
43. Lobe S, Bauer A, Uhlenbruck S, Fattakhova-Rohlfing D. Physical vapor deposition in solid-state battery development: from materials to devices. Adv Sci 2021;8:e2002044.
44. Zeng L, Li P, Yao Y, Niu B, Niu S, Xu B. Recent progresses of 3D printing technologies for structural energy storage devices. Mater Today Nano 2020;12:100094.
45. Zhang F, Wei M, Viswanathan VV, et al. 3D printing technologies for electrochemical energy storage. Nano Energy 2017;40:418-31.
46. Egorov V, Gulzar U, Zhang Y, Breen S, O'Dwyer C. Evolution of 3D printing methods and materials for electrochemical energy storage. Adv Mater 2020;32:e2000556.
47. Cheng M, Deivanayagam R, Shahbazian-yassar R. 3D printing of electrochemical energy storage devices: a review of printing techniques and electrode/electrolyte architectures. Batteries Supercaps 2020;3:130-46.
48. Gao T, Zhou Z, Yu J, et al. 3D printing of tunable energy storage devices with both high areal and volumetric energy densities. Adv Energy Mater 2019;9:1802578.
49. Guo B, Liang G, Yu S, Wang Y, Zhi C, Bai J. 3D printing of reduced graphene oxide aerogels for energy storage devices: a paradigm from materials and technologies to applications. Energy Stor Mater 2021;39:146-65.
50. Guo H, Lv R, Bai S. Recent advances on 3D printing graphene-based composites. Nano Mater Sci 2019;1:101-15.
51. Wang J, Liu Y, Fan Z, Wang W, Wang B, Guo Z. Ink-based 3D printing technologies for graphene-based materials: a review. Adv Compos Hybrid Mater 2019;2:1-33.
52. Pang Y, Cao Y, Chu Y, et al. Additive manufacturing of batteries. Adv Funct Mater 2020;30:1906244.
53. Tagliaferri S, Panagiotopoulos A, Mattevi C. Direct ink writing of energy materials. Mater Adv 2021;2:540-63.
54. Tian X, Jin J, Yuan S, Chua CK, Tor SB, Zhou K. Emerging 3D-printed electrochemical energy storage devices: a critical review. Adv Energy Mater 2017;7:1700127.
55. Xu X, Tan YH, Ding J, Guan C. 3D printing of next-generation electrochemical energy storage devices: from multiscale to multimaterial. Energy Environ Mater 2022;5:427-38.
56. Zhu C, Liu T, Qian F, et al. 3D printed functional nanomaterials for electrochemical energy storage. Nano Today 2017;15:107-20.
57. Yao B, Chandrasekaran S, Zhang J, et al. Efficient 3D printed pseudocapacitive electrodes with ultrahigh MnO2 loading. Joule 2019;3:459-70.
58. Zeng L, Ling S, Du D, He H, Li X, Zhang C. Direct ink writing 3D printing for high-performance electrochemical energy storage devices: a minireview. Adv Sci 2023;10:2303716.
59. Wei M, Zhang F, Wang W, Alexandridis P, Zhou C, Wu G. 3D direct writing fabrication of electrodes for electrochemical storage devices. Jops 2017;354:134-47.
60. Lyu Z, Lim GJ, Koh JJ, et al. Design and manufacture of 3D-printed batteries. Joule 2021;5:89-114.
61. Kim H, Johnson J, Chavez LA, Garcia Rosales CA, Tseng TB, Lin Y. Enhanced dielectric properties of three phase dielectric MWCNTs/BaTiO3/PVDF nanocomposites for energy storage using fused deposition modeling 3D printing. Ceram Int 2018;44:9037-44.
62. Maurel A, Russo R, Grugeon S, Panier S, Dupont L. Environmentally friendly lithium-terephthalate/polylactic acid composite filament formulation for lithium-ion battery 3D-printing via fused deposition modeling. ECS J Solid State Sci Technol 2021;10:037004.
63. Sztymela K, Bienia M, Rossignol F, et al. Fabrication of modern lithium ion batteries by 3D inkjet printing: opportunities and challenges. Heliyon 2022;8:e12623.
64. Pei M, Shi H, Yao F, et al. 3D printing of advanced lithium batteries: a designing strategy of electrode/electrolyte architectures. J Mater Chem A 2021;9:25237-57.
65. Gulzar U, Glynn C, O'dwyer C. Additive manufacturing for energy storage: methods, designs and material selection for customizable 3d printed batteries and supercapacitors. Curr Opin Electroche 2020;20:46-53.
66. Gokhare VG, Raut DN, Shinde DK. A review paper on 3D-printing aspects and various processes used in the 3D-printing. Available from: https://www.ijert.org/a-review-paper-on-3d-printing-aspects-and-various-processes-used-in-the-3d-printing [Last accessed on 7 Mar 2024].
67. Ge Q, Li Z, Wang Z, et al. Projection micro stereolithography based 3D printing and its applications. Int J Extrem Manuf 2020;2:022004.
68. Katsuyama Y, Haba N, Kobayashi H, et al. Macro- and nano-porous 3D-hierarchical carbon lattices for extraordinarily high capacitance supercapacitors. Adv Funct Mater 2022;32:2201544.
69. Li L, Deng Z, Chen M, Yu ZZ, Russell TP, Zhang HB. 3D Printing of ultralow-concentration 2D nanomaterial inks for multifunctional architectures. Nano Lett 2023;23:155-62.
70. Sahoo R, Pal A, Pal T. 2D materials for renewable energy storage devices: outlook and challenges. Chem Commun 2016;52:13528-42.
71. Dong Y, Wu ZS, Ren W, Cheng HM, Bao X. Graphene: a promising 2D material for electrochemical energy storage. Sci Bull 2017;62:724-40.
72. Wang L, Chen S, Shu T, Hu X. Functional Inks for printable energy storage applications based on 2D materials. ChemSusChem 2020;13:1330-53.
73. Naficy S, Jalili R, Aboutalebi SH, et al. Graphene oxide dispersions: tuning rheology to enable fabrication. Mater Horiz 2014;1:326-31.
74. Jiang Y, Guo F, Liu Y, Xu Z, Gao C. Three-dimensional printing of graphene-based materials for energy storage and conversion. SusMat 2021;1:304-23.
76. Xie Y, Zhang H, Huang H, et al. High-voltage asymmetric MXene-based on-chip micro-supercapacitors. Nano Energy 2020;74:104928.
77. Zhu Y, Wang S, Ma J, Das P, Zheng S, Wu Z. Recent status and future perspectives of 2D MXene for micro-supercapacitors and micro-batteries. Energy Stor Mater 2022;51:500-26.
78. Zhang CJ, McKeon L, Kremer MP, et al. Additive-free MXene inks and direct printing of micro-supercapacitors. Nat Commun 2019;10:1795.
79. Yang W, Yang J, Byun JJ, et al. 3D printing of freestanding MXene architectures for current-collector-free supercapacitors. Adv Mater 2019;31:e1902725.
80. Akuzum B, Maleski K, Anasori B, et al. Rheological characteristics of 2D titanium carbide (MXene) dispersions: a guide for processing MXenes. ACS Nano 2018;12:2685-94.
81. Bao C, Zhang H, Wilkie CA, et al. On the dispersion systems of graphene-like two-dimensional materials: From fundamental laws to engineering guidelines. Carbon 2016;107:774-82.
82. García-Tuñón E, Feilden E, Zheng H, D'Elia E, Leong A, Saiz E. Graphene oxide: an all-in-one processing additive for 3D printing. ACS Appl Mater Interfaces 2017;9:32977-89.
83. Panagiotopoulos A, Nagaraju G, Tagliaferri S, et al. 3D printed inks of two-dimensional semimetallic MoS2 /TiS2 nanosheets for conductive-additive-free symmetric supercapacitors. J Mater Chem A 2023;11:16190-200.
84. Zhou G, Li M, Liu C, Wu Q, Mei C. 3D printed Ti3C2 TxMXene/cellulose nanofiber architectures for solid-state supercapacitors: ink rheology, 3D printability, and electrochemical performance. Adv Funct Mater 2022;32:2109593.
85. Tang X, Zhou H, Cai Z, et al. Generalized 3D printing of graphene-based mixed-dimensional hybrid aerogels. ACS Nano 2018;12:3502-11.
86. Yao B, Chandrasekaran S, Zhang H, et al. 3D-printed structure boosts the kinetics and intrinsic capacitance of pseudocapacitive graphene aerogels. Adv Mater 2020;32:e1906652.
87. Zheng Y, Zhao W, Jia D, Cui L, Liu J. Thermally-treated and acid-etched carbon fiber cloth based on pre-oxidized polyacrylonitrile as self-standing and high area-capacitance electrodes for flexible supercapacitors. Chem Eng J 2019;364:70-8.
88. Zhu C, Liu T, Qian F, et al. Supercapacitors based on three-dimensional hierarchical graphene aerogels with periodic macropores. Nano Lett 2016;16:3448-56.
89. Chandrasekaran S, Yao B, Liu T, et al. Direct ink writing of organic and carbon aerogels. Mater Horiz 2018;5:1166-75.
90. Wang G, Wang H, Lu X, et al. Solid-state supercapacitor based on activated carbon cloths exhibits excellent rate capability. Adv Mater 2014;26:2676-82, 2615.
91. Wang Y, Zhang Y, Wang G, et al. Direct graphene-carbon nanotube composite ink writing all-solid-state flexible microsupercapacitors with high areal energy density. Adv Funct Mater 2020;30:1907284.
92. Nakhanivej P, Dou Q, Xiong P, Park HS. Two-dimensional pseudocapacitive nanomaterials for high-energy- and high-power-oriented applications of supercapacitors. ACC Mater Res 2021;2:86-96.
93. Kyeremateng NA, Brousse T, Pech D. Microsupercapacitors as miniaturized energy-storage components for on-chip electronics. Nat Nanotechnol 2017;12:7-15.
94. Kamboj N, Purkait T, Das M, Sarkar S, Hazra KS, Dey RS. Ultralong cycle life and outstanding capacitive performance of a 10.8 V metal free micro-supercapacitor with highly conducting and robust laser-irradiated graphene for an integrated storage device. Energy Environ Sci 2019;12:2507-17.
95. Jiang Y, Xu Z, Huang T, et al. Direct 3D printing of ultralight graphene oxide aerogel microlattices. Adv Funct Mater 2018;28:1707024.
96. Bhojane P. Recent advances and fundamentals of pseudocapacitors: materials, mechanism, and its understanding. J Energy Stor 2022;45:103654.
97. Kim HS, Cook JB, Lin H, et al. Oxygen vacancies enhance pseudocapacitive charge storage properties of MoO3-x. Nat Mater 2017;16:454-60.
98. Wang Y, Wang M, Wang P, et al. Urea-treated wet-spun PEDOT: PSS fibers for achieving high-performance wearable supercapacitors. Compos Commun 2021;27:100885.
99. Augustyn V, Simon P, Dunn B. Pseudocapacitive oxide materials for high-rate electrochemical energy storage. Energy Environ Sci 2014;7:1597.
100. Lai F, Miao YE, Huang Y, Zhang Y, Liu T. Nitrogen-doped carbon nanofiber/molybdenum disulfide nanocomposites derived from bacterial cellulose for high-efficiency electrocatalytic hydrogen evolution reaction. ACS Appl Mater Interfaces 2016;8:3558-66.
101. Saeed G, Bandyopadhyay P, Kumar S, Kim NH, Lee JH. ZnS-Ni7S6 nanosheet arrays wrapped with nanopetals of Ni(OH)2 as a novel core-shell electrode material for asymmetric supercapacitors with high energy density and cycling stability performance. ACS Appl Mater Interfaces 2020;12:47377-88.
102. Alam A, Saeed G, Lim S. One-step synthesis of 2D-2D Co(OH)2-MoSe2 hybrid nanosheets as an efficient electrode material for high-performance asymmetric supercapacitor. J Electroanal Chem 2020;879:114775.
103. Kumar KS, Choudhary N, Jung Y, Thomas J. Recent advances in two-dimensional nanomaterials for supercapacitor electrode applications. ACS Energy Lett 2018;3:482-95.
104. Zong W, Ouyang Y, Miao YE, Liu T, Lai F. Recent advances and perspectives of 3D printed micro-supercapacitors: from design to smart integrated devices. Chem Commun 2022;58:2075-95.
105. Huang X, Huang J, Yang D, Wu P. A multi-scale structural engineering strategy for high-performance MXene hydrogel supercapacitor electrode. Adv Sci 2021;8:e2101664.
106. Yao B, Peng H, Zhang H, et al. Printing porous carbon aerogels for low temperature supercapacitors. Nano Lett 2021;21:3731-7.
107. Yu L, Fan Z, Shao Y, Tian Z, Sun J, Liu Z. Versatile N-doped MXene ink for printed electrochemical energy storage application. Adv Energy Mater 2019;9:1901839.
108. Orangi J, Hamade F, Davis VA, Beidaghi M. 3D printing of additive-free 2D Ti3C2Tx (MXene) ink for fabrication of micro-supercapacitors with ultra-high energy densities. ACS Nano 2020;14:640-50.
109. Sadavar S, Wang KJ, Kang T, et al. Anion storage for hybrid supercapacitor. Mater Today Energy 2023;37:101388.
110. Zhao J, Zhang Y, Lu H, et al. Additive manufacturing of two-dimensional conductive metal-organic framework with multidimensional hybrid architectures for high-performance energy storage. Nano Lett 2022;22:1198-206.
111. Yang Z, Yang X, Yang T, et al. 3D printing of carbon tile-modulated well-interconnected hierarchically porous pseudocapacitive electrode. Energy Stor Mater 2023;54:51-9.
112. Zhao J, Zhang Y, Zhao X, et al. Direct ink writing of adjustable electrochemical energy storage device with high gravimetric energy densities. Adv Funct Mater 2019;29:1900809.
113. Zhang C, Kremer MP, Seral-ascaso A, et al. Stamping of flexible, coplanar micro-supercapacitors using MXene inks. Adv Funct Mater 2018;28:1705506.
114. Zhao Y, Liu F, Zhu K, Maganti S, Zhao Z, Bai P. Three-dimensional printing of the copper sulfate hybrid composites for supercapacitor electrodes with ultra-high areal and volumetric capacitances. Adv Compos Hybrid Mater 2022;5:1537-47.
115. Pender JP, Jha G, Youn DH, et al. Electrode degradation in lithium-ion batteries. ACS Nano 2020;14:1243-95.
116. Chen C, Jiang M, Zhou T, et al. Interface aspects in all-solid-state Li-based batteries reviewed. Adv Energy Mater 2021;11:2003939.
117. Imanishi N, Yamamoto O. Rechargeable lithium-air batteries: characteristics and prospects. Mater Today 2014;17:24-30.
118. Yang R, Zhou J, Yang C, Qiu L, Cheng H. Recent progress in 3D printing of 2D material-based macrostructures. Adv Mater Tech 2020;5:1901066.
119. Ye J, Baumgaertel AC, Wang YM, Biener J, Biener MM. Structural optimization of 3D porous electrodes for high-rate performance lithium ion batteries. ACS Nano 2015;9:2194-202.
120. Zhang H, Yu X, Braun PV. Three-dimensional bicontinuous ultrafast-charge and -discharge bulk battery electrodes. Nat Nanotechnol 2011;6:277-81.
121. Hassan K, Nine MJ, Tung TT, et al. Functional inks and extrusion-based 3D printing of 2D materials: a review of current research and applications. Nanoscale 2020;12:19007-42.
122. Sun C, Liu S, Shi X, Lai C, Liang J, Chen Y. 3D printing nanocomposite gel-based thick electrode enabling both high areal capacity and rate performance for lithium-ion battery. Chem Eng J 2020;381:122641.
123. Rosenman A, Markevich E, Salitra G, Aurbach D, Garsuch A, Chesneau FF. Review on Li-sulfur battery systems: an integral perspective. Adv Energy Mater 2015;5:1500212.
124. Shen K, Mei H, Li B, Ding J, Yang S. 3D printing sulfur copolymer-graphene architectures for Li-S batteries. Adv Energy Mater 2018;8:1701527.
125. Chen C, Jiang J, He W, Lei W, Hao Q, Zhang X. 3D printed high-loading lithium-sulfur battery toward wearable energy storage. Adv Funct Mater 2020;30:1909469.
127. Ma J, Zheng S, Zhou F, et al. All 3D printing lithium metal batteries with hierarchically and conductively porous skeleton for ultrahigh areal energy density. Energy Stor Mater 2023;54:304-12.
128. Shen K, Cao Z, Shi Y, Zhang Y, Li B, Yang S. 3D printing lithium salt towards dendrite-free lithium anodes. Energy Stor Mater 2021;35:108-13.
129. Lyu Z, Lim GJ, Guo R, et al. 3D-printed electrodes for lithium metal batteries with high areal capacity and high-rate capability. Energy Stor Mater 2020;24:336-42.
130. Gao X, Yang X, Wang S, et al. A 3D-printed ultra-high Se loading cathode for high energy density quasi-solid-state Li-Se batteries. J Mater Chem A 2020;8:278-86.
131. Cai J, Jin J, Fan Z, et al. 3D Printing of a V8C7-VO2 Bifunctional scaffold as an effective polysulfide immobilizer and lithium stabilizer for Li-S batteries. Adv Mater 2020;32:e2005967.
132. Mubarak S, Dhamodharan D, Byun H. Recent advances in 3D printed electrode materials for electrochemical energy storage devices. J Energy Chem 2023;81:272-312.
133. Bu F, Li C, Wang Q, Liu X. Ultraviolet-assisted printing of flexible all-solid-state zinc batteries with enhanced interfacial bond. Chem Eng J 2022;449:137710.
134. Hwang JY, Myung ST, Sun YK. Sodium-ion batteries: present and future. Chem Soc Rev 2017;46:3529-614.
135. Zhang T, Tang Y, Guo S, et al. Fundamentals and perspectives in developing zinc-ion battery electrolytes: a comprehensive review. Energy Environ Sci 2020;13:4625-65.
136. Jia X, Liu C, Neale ZG, Yang J, Cao G. Active materials for aqueous zinc ion batteries: synthesis, crystal structure, morphology, and electrochemistry. Chem Rev 2020;120:7795-866.
137. Lourenssen K, Williams J, Ahmadpour F, Clemmer R, Tasnim S. Vanadium redox flow batteries: a comprehensive review. J Energy Stor 2019;25:100844.
138. Zhu Y, Peng L, Fang Z, Yan C, Zhang X, Yu G. Structural engineering of 2D nanomaterials for energy storage and catalysis. Adv Mater 2018;30:e1706347.
139. Pomerantseva E, Bonaccorso F, Feng X, Cui Y, Gogotsi Y. Energy storage: the future enabled by nanomaterials. Science 2019;366:eaan8285.
140. Wang Z, Huang Z, Wang H, et al. 3D-printed sodiophilic V2CTx/rGO-CNT MXene microgrid aerogel for stable Na metal anode with high areal capacity. ACS Nano 2022;16:9105-16.
141. Li Q, Dong Q, Wang J, et al. Direct ink writing (DIW) of graphene aerogel composite electrode for vanadium redox flow battery. Jops 2022;542:231810.
142. Ma H, Tian X, Wang T, et al. Tailoring pore structures of 3D printed cellular high-loading cathodes for advanced rechargeable Zinc-Ion batteries. Small 2021;17:e2100746.
143. Yang H, Wang H, Li W, et al. A simple and effective host for sodium metal anode: a 3D-printed high pyrrolic-N doped graphene microlattice aerogel. J Mater Chem A 2022;10:16842-52.
144. Ma J, Zheng S, Chi L, et al. 3D printing flexible sodium-ion microbatteries with ultrahigh areal capacity and robust rate capability. Adv Mater 2022;34:e2205569.
Cite This Article
Export citation file: BibTeX | RIS
OAE Style
Saeed G, Kang T, Byun JS, Min D, Kim JS, Sadavar SV, Park HS. Two-dimensional (2D) materials for 3D printed micro-supercapacitors and micro-batteries. Energy Mater 2024;4:400023. http://dx.doi.org/10.20517/energymater.2023.81
AMA Style
Saeed G, Kang T, Byun JS, Min D, Kim JS, Sadavar SV, Park HS. Two-dimensional (2D) materials for 3D printed micro-supercapacitors and micro-batteries. Energy Materials. 2024; 4(3): 400023. http://dx.doi.org/10.20517/energymater.2023.81
Chicago/Turabian Style
Saeed, Ghuzanfar, Taehun Kang, Jin Suk Byun, Donghyun Min, Jun Su Kim, Shrikant Vaiju Sadavar, Ho Seok Park. 2024. "Two-dimensional (2D) materials for 3D printed micro-supercapacitors and micro-batteries" Energy Materials. 4, no.3: 400023. http://dx.doi.org/10.20517/energymater.2023.81
ACS Style
Saeed, G.; Kang T.; Byun JS.; Min D.; Kim JS.; Sadavar SV.; Park HS. Two-dimensional (2D) materials for 3D printed micro-supercapacitors and micro-batteries. Energy Mater. 2024, 4, 400023. http://dx.doi.org/10.20517/energymater.2023.81
About This Article
Special Issue
Copyright
Data & Comments
Data
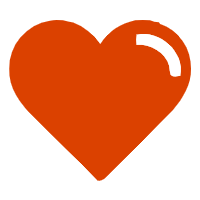

Comments
Comments must be written in English. Spam, offensive content, impersonation, and private information will not be permitted. If any comment is reported and identified as inappropriate content by OAE staff, the comment will be removed without notice. If you have any queries or need any help, please contact us at support@oaepublish.com.